Transformer Installation Case Studies
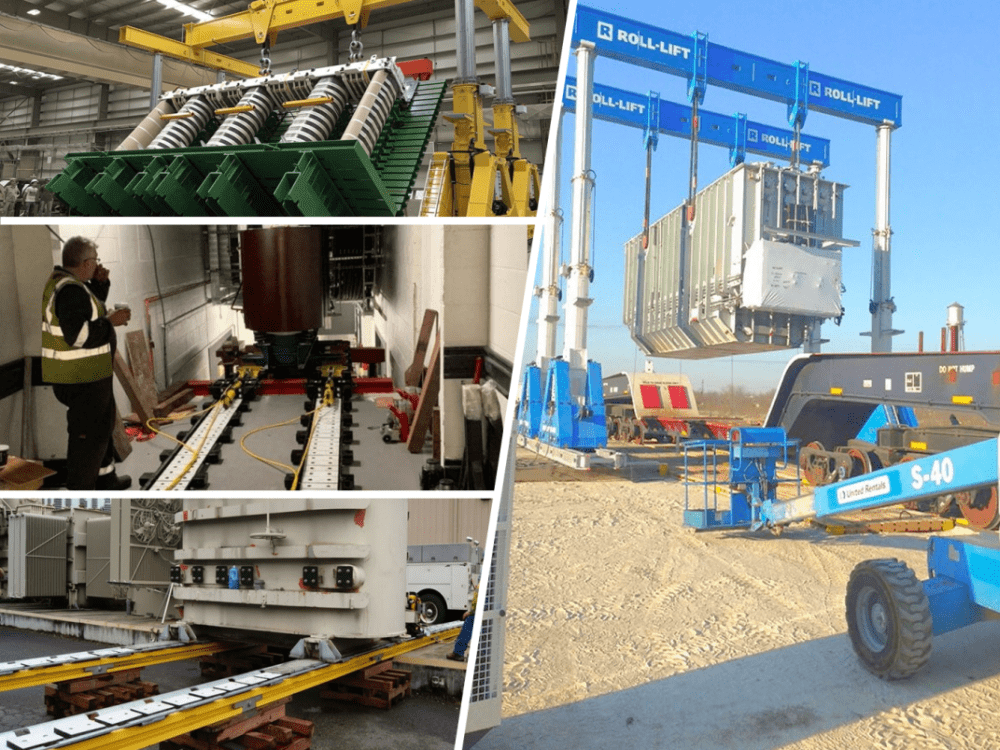
August 11, 2022
0
Transformer installation is not for the faint-hearted. It requires careful planning, experienced and skilled staff, and the right equipment.
There’s no escaping the fact that transformers are incredibly heavy. A typical transformer contains a core made from many layers of laminated steel, a huge amount of wire for metal windings, insulating materials and mineral oil. Add to that the exterior steel casing and you can see why transformers can weigh hundreds of tons.
Lets’ take a look at five examples where hydraulic equipment helped towards a successful outcome.
Transformer Installation: Lifting from a Railcar onto a Heavy Haul Truck
From manufacture to installation on-site, there are several transportation stages a transformer may undergo. Each of these steps has different needs, and that can include moving the transformer from one mode of transport to another. Completing this safely takes careful planning and the right choice of equipment.
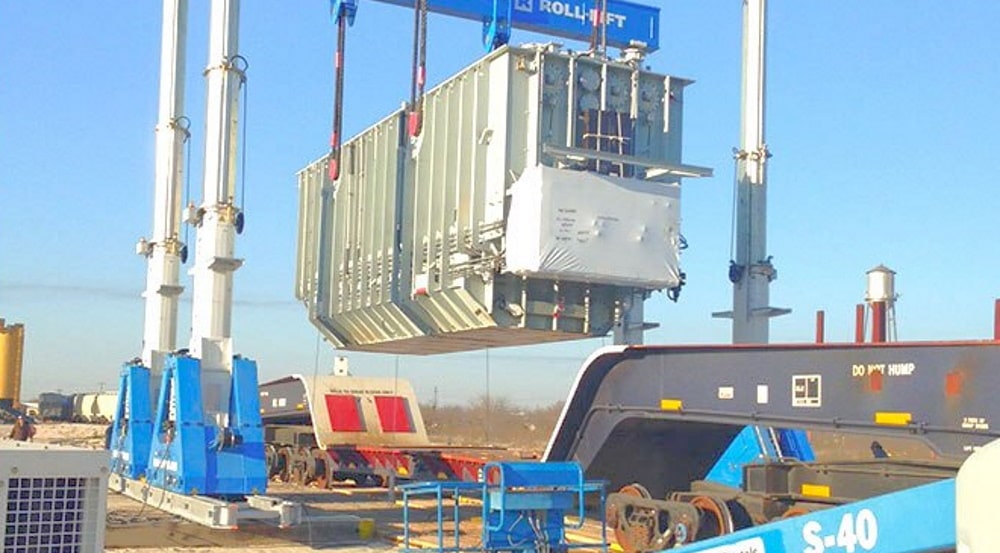
Heavy lifting company Roll-Lift was tasked with transporting and installing a new 330-ton transformer at a sub-station in San Angelo, Texas. An important step in the process was to transfer the transformer from a drop deck railcar onto a heavy haul truck to take it to its final destination.
This was achieved using an SBL900 Hydraulic Gantry. This model includes an octagonal sectioned foldable boom for added strength and convenient transport.
Hydraulic Gantry For Transformer Manufacturing
Before installation or removal, transformers also need to move during the manufacturing process.
One manufacturer, Tadeo Czerweny, decided to expand its capacity to build larger higher-capacity transformers.
Achieving this required raising a heavy platform structure for assembling electric transformer cores and transport within their plant.
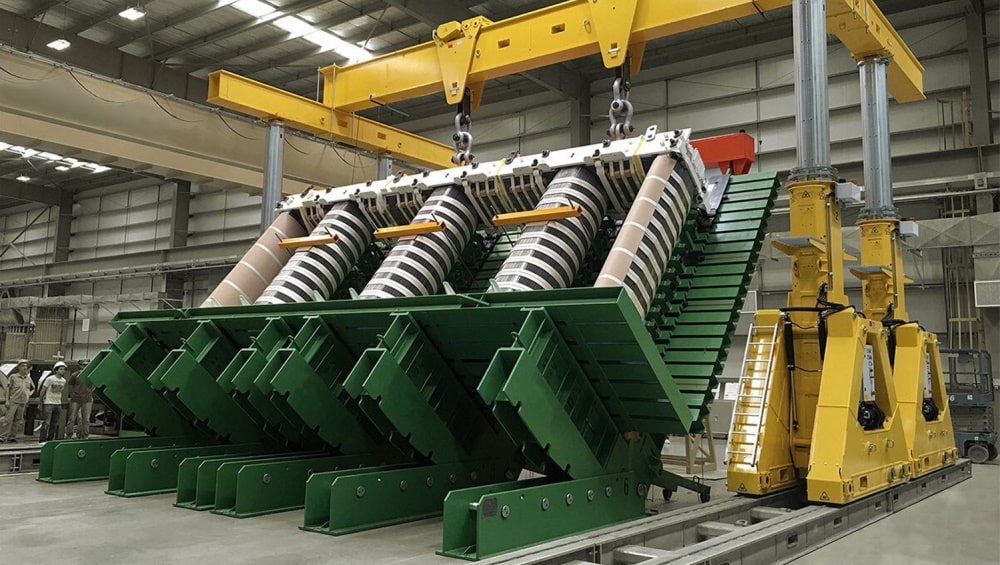
The loads weighed from 250 to 300 metric tons and measured 36 ft (11 meters) high. The Enerpac SBL1100 was selected as the optimum hydraulic gantry, as this provides the accuracy, control, and flexibility to suit different operations throughout the transformer manufacturing process.
Transformer Installation and Removal for Maintenance or Replacement
In the event of a power outage, a transformer may need maintenance or replacing. This can involve several workers operating different pieces of equipment.
An Enerpac customer in the United States, The Bonneville Power Administration (BPA), wanted to source equipment that would simplify and improve the safety of their existing process. Quite often, the space around a transformer in-situ can be incredibly tight, which often rules out cranes or gantries.
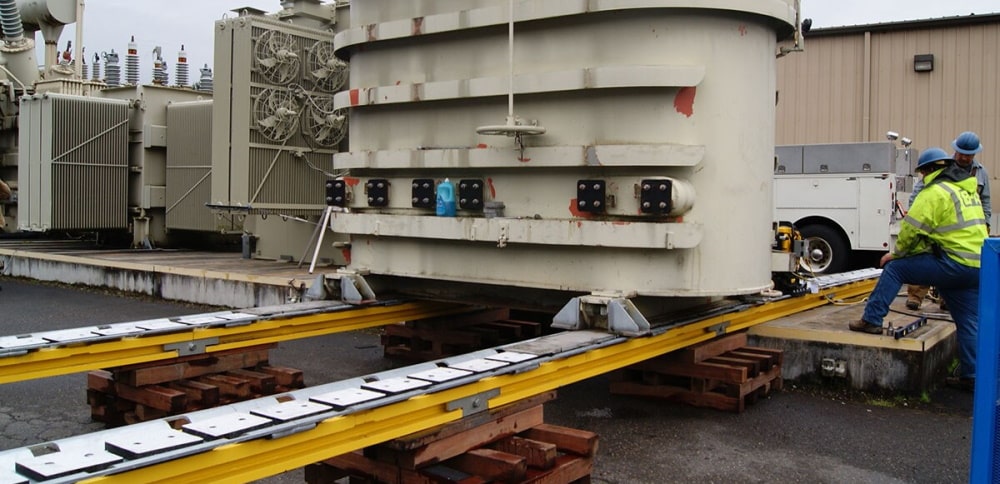
The solution chosen by BPA was to use a custom Enerpac Hydraulic Skidding System. A typical skidding system includes a pre-constructed track with special PTFE-coated pads to reduce friction. The force for skidding the load is provided by push-pull hydraulic cylinders powered by hydraulic pumps. A significant benefit of a skidding system is that it provides a single operator with the ability to position their load precisely with push button control.
Transformer Removal and Replacement in a Restricted Area
As mentioned in the previous example, moving a transformer from its installed location can be extra challenging when space is restricted. If the transformer is inside a building space with low headroom this presents even more difficulties to overcome.
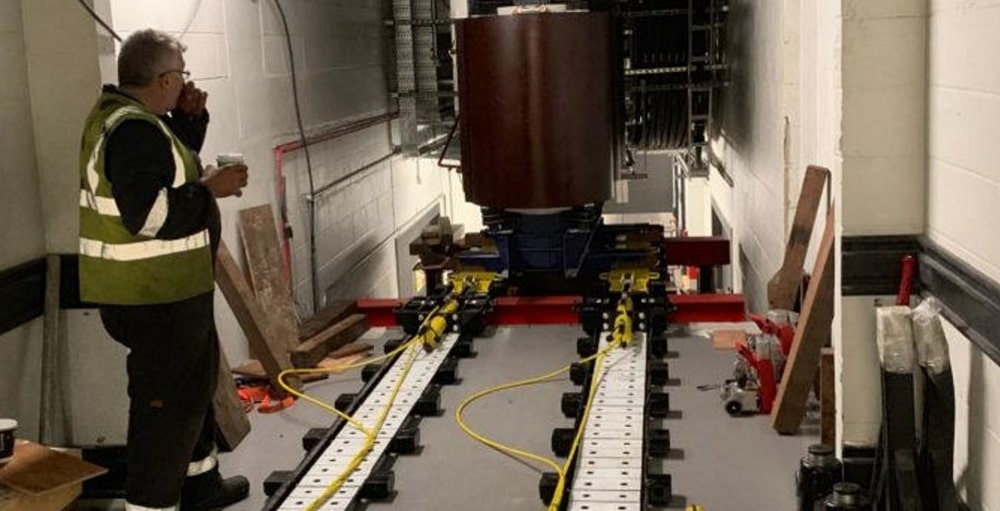
The picture above shows an example where four 16-ton transformers needed to be removed from the basement of a building in the UK. Each transformer was 13 ft (4m) long, 7 ft (2.2m) high, and 6ft (1.8m) wide. The project involved moving them along a 65 ft (20m) access corridor and negotiating a 10 ft (3m) drop.
The equipment used by heavy machine lifting company, D. Turner & Son included an Enerpac LH400 Skidding System, Enerpac Climbing Jacks, and a Split-Flow Pump.
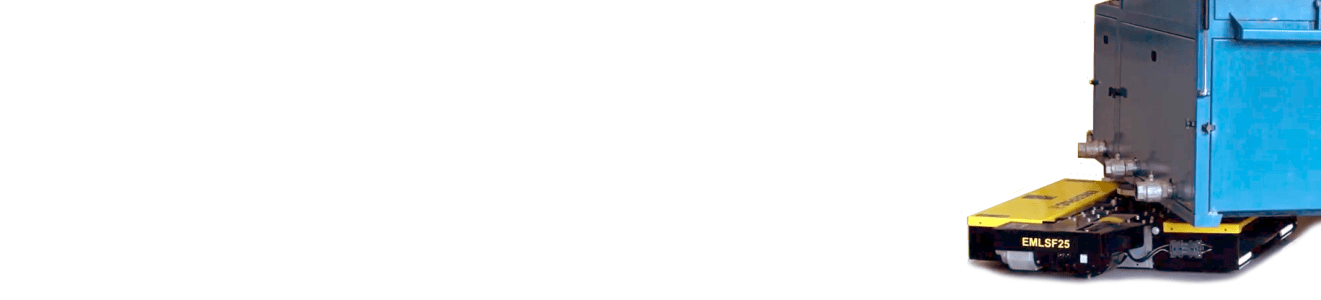
Machine Mover’s Virtual Tool Room
Everything you need in one place
Weighing a Transformer Before Transporting Overseas
Transporting transformers long distances by sea can incur high shipping costs – especially if they exceed the port’s maximum weight limits. Therefore, it is vital to know the weight of the transformer before making any shipping arrangements. One example illustrating this point was when a heavy lift company, Machine Movers. The company was tasked with sending a transformer from New Zealand to India. The port in New Zealand had a 110-ton maximum lifting capacity. So anything heavier would need a special ship to be brought in – with significant freight costs.
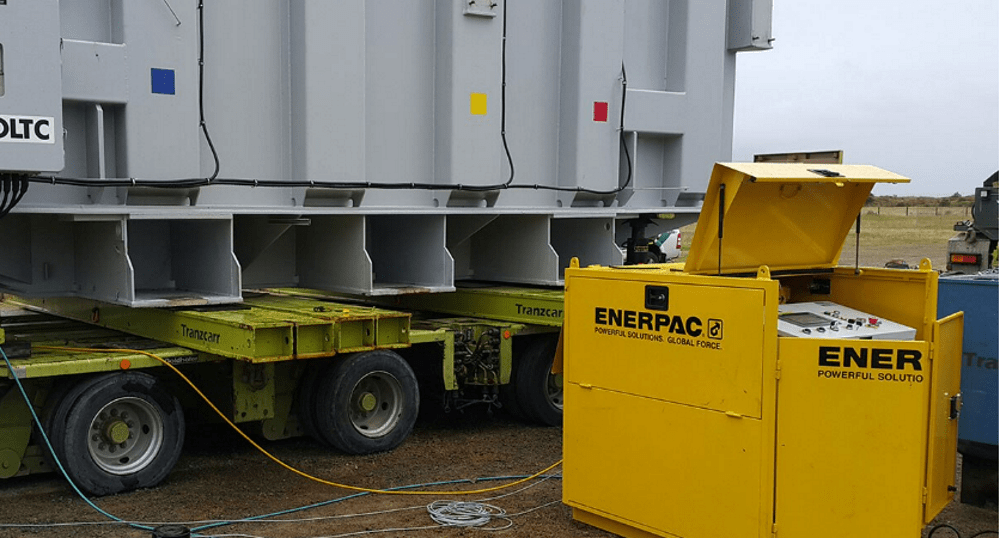
Weighing a 100-ton transformer is no mean feat and therefore requires specialist equipment. The Enerpac EVO Synchronous Lift System with four RACL-Series aluminum lock nut hydraulic cylinders was identified as the best solution.
This uses calibrated pressure transducers to send the weigh data to the EVO system from where it can be downloaded. The transformer was weighed 5 times, and the average weight was calculated as 109.4 tons. This was under the local shipping port’s weight limits so significant freight costs were avoided.
Learn more about the EVO Synchronous Lifting System