Maglev Trains vs Conventional: The Key Differences
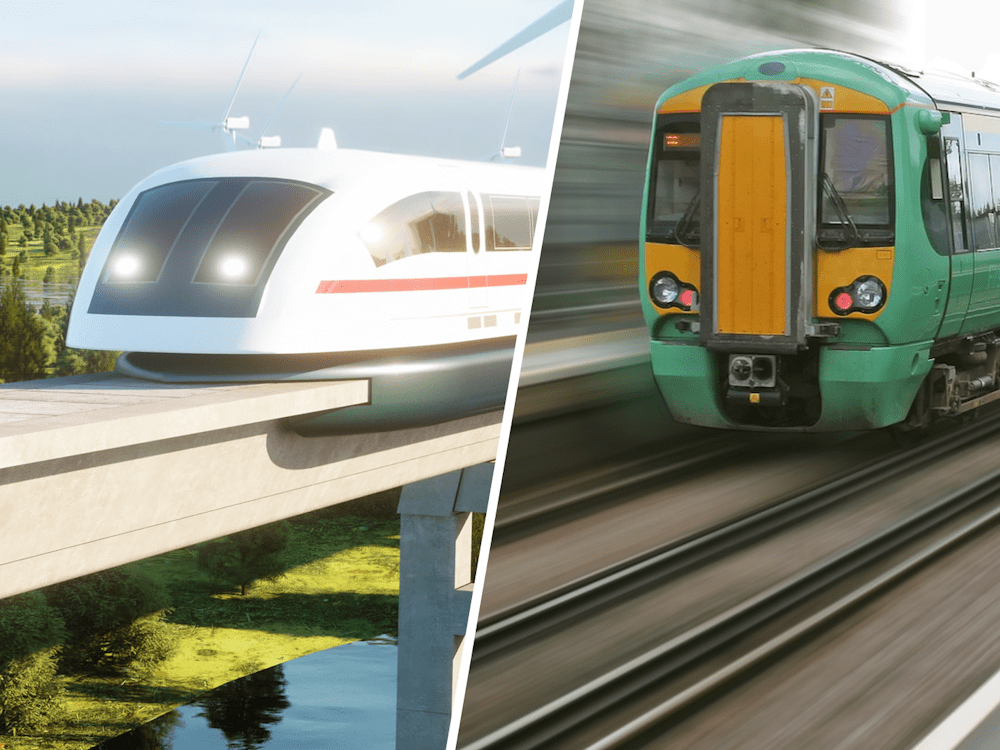
September 9, 2024
0
Maintaining transportation infrastructure is crucial for safety, reliability, and operational efficiency. Two distinct approaches to rail transport—magnetic levitation (maglev) trains and conventional rail systems present fascinating contrasts in maintenance requirements and challenges. This article explores how these technologies differ in their upkeep needs and what this means for operators and passengers worldwide.
But first, here’s a quick overview of Maglev Trains.
Maglev Trains
What are Maglev Trains?
Maglev, short for magnetic levitation, is an advanced rail transport technology where trains float above the track using powerful electromagnets. This revolutionary system eliminates the need for wheels, axles, and bearings, resulting in a frictionless and ultra-fast mode of transportation.
How Do Maglev Trains Work?
The principle of magnetic levitation (maglev) for transport has been around since the 1960s when Professor Eric Laithwaite, a pioneering British electrical engineer, developed the linear induction motor and demonstrated the concept of magnetic levitation as a possibility for transportation.
Maglev trains operate on two main principles:
- Electromagnetic Suspension (EMS): Uses electromagnets to lift the train
- Electrodynamic Suspension (EDS): Utilizes superconducting magnets for levitation at high speeds
Maglev Trains Speed
The Shanghai maglev train has a top operational speed of 431 kilometers per hour (268 miles per hour). However, the L0 Series Maglev in Japan holds the record for the fastest train in the world, reaching a speed of 603 kilometers per hour (375 miles per hour) in 2015.
Advantages of Magnetic Levitation Trains
A maglev system delivers unmistakable benefits:
Maglev Speeds: With friction reduced to near zero, maglev train speeds are impressive. The fastest commercial system is capable of reaching 430 km/h (267 mph), significantly cutting travel times compared to conventional trains. However, the L0 Series Maglev in Japan holds the record for the fastest train in the world, reaching a speed of 603 kilometers per hour (375 miles per hour) in 2015.
Lower Maintenance: Since there is no direct contact between the train and the track, wear and tear on both components are minimal, reducing the need for constant repairs and maintenance. (Note that EDS maglev systems rely on small wheels when traveling at low speeds).
Quieter Operation: The absence of wheels and track noise make maglev trains a quieter and more comfortable travel option than traditional trains.
Smoother Ride: The floating nature of maglev systems ensures a smooth, vibration-free ride without the bumps typical of traditional rail systems.
Safety: Maglev trains are less prone to derailments or accidents caused by physical damage to tracks, offering a safer travel experience.
Maglev Use Cases Across the World
As it stands, maglev trains have been running for several decades, but there are still only six operational maglev train lines in the world today: three in China, two in South Korea, and one in Japan.
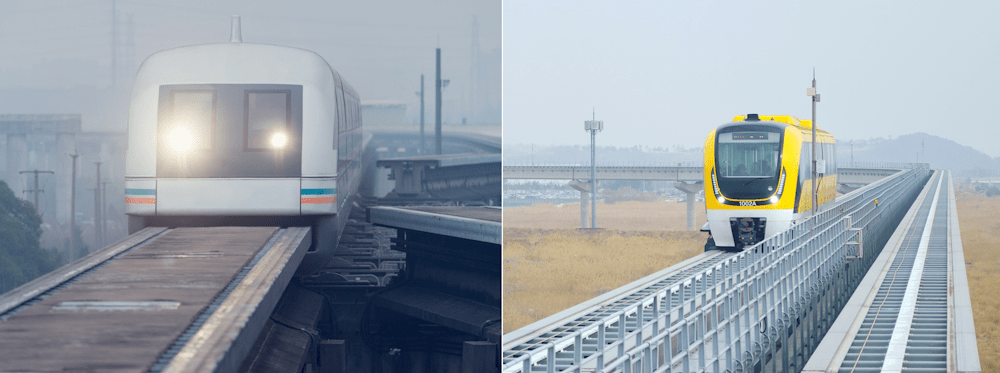
Some Current Maglev Train Projects
- Shanghai Maglev Train (operational since 2004)
- Yeongjongo island, South Korea
- Japan’s Chūō Shinkansen (under construction)
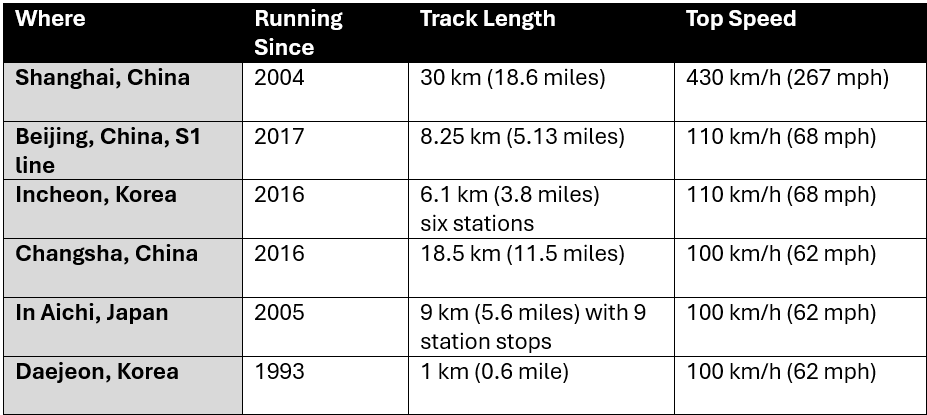

Track Maintenance Comparison
Maglev Trains: Guideway Maintenance
Maglev trains float above their guideways using magnetic forces, eliminating direct physical contact between the vehicle and track. This fundamental difference creates unique maintenance characteristics:
- Precision alignment: Maglev guideways demand extremely tight tolerances—typically within millimeters—to maintain proper magnetic field interactions. Specialized laser alignment systems and measurement tools are used during regular inspections.
- Surface quality monitoring: The guideway surface must remain perfectly smooth to maintain consistent levitation gaps. Technicians use optical scanning equipment to detect even minor surface imperfections.
- Expansion joint management: Thermal expansion and contraction must be precisely managed through specialized expansion joints that maintain perfect alignment while allowing for movement.
- Guideway cleaning operations: Without regular cleaning, dust and debris can interfere with magnetic field efficiency. Automated cleaning vehicles run during off-hours, using vacuum systems and specialized brushes to maintain pristine surfaces.
- Structural monitoring: Sensors embedded throughout the guideway continuously monitor for settlement, vibration, and structural integrity. Even small shifts in alignment can affect system performance
Conventional Track Maintenance
Traditional rail networks worldwide rely on steel-on-steel technology with ballasted or slab track designs, requiring a completely different maintenance approach:
- Rail grinding programs: Rail networks implement cyclical rail grinding to remove surface defects, correct rail profile, and extend rail life. High-speed lines typically require grinding every 15-30 million gross tons of traffic.
- Rail stressing operations: A critical maintenance activity unique to conventional rail, rail stressing ensures tracks maintain the correct tension to prevent buckling in hot weather (sun kinks) and breakage in cold conditions.
Rail workers typically carry out these activities:
- Install continuously welded rail (CWR) at a “stress-free temperature” (typically 21-27°C in temperate regions)
- Use hydraulic tensioners to achieve precise stress levels during installation
- Perform regular stress measurements using specialized equipment
- Conduct “de-stressing” operations when tracks show signs of incorrect stress levels
- Monitor critical locations with rail temperature sensors that trigger speed restrictions during extreme weather
- Schedule preventive stressing work during moderate temperature seasons
Ballast management: For ballasted track, regular tamping and ballast cleaning are essential. The stone ballast bed gradually deteriorates due to crushing and contamination, requiring periodic renewal to maintain drainage and track geometry.
Fastening system inspection: The clips, bolts, and other components that secure rails to sleepers require regular inspection and replacement. On high-speed lines, loose fasteners can quickly lead to dangerous conditions.
Switch and crossing maintenance: These complex components experience intense forces and wear. Rail networks typically have specialized teams dedicated solely to switch maintenance with strict inspection protocols.
Track geometry correction: Track recording vehicles regularly measure parameters like gauge, alignment, and cant. When values exceed tolerance, maintenance teams deploy tamping machines to restore geometry.
Advanced Maintenance Technologies
Magnetic Levitation Track Technologies
- Non-contact inspection systems: Maglev operators employ electromagnetic and optical sensors to inspect guideway components without physical contact, preserving the precise alignments.
- Predictive analytics: Extensive sensor networks throughout maglev guideways feed data to AI systems that can predict potential failures before they occur, allowing for precisely scheduled preventive maintenance.
- Modular component design: Many maglev systems utilize modular guideway components that can be quickly replaced during maintenance windows, minimizing service disruptions.
Conventional Track Technologies
- High-speed measuring trains: Major rail networks operate specialized diagnostic trains that can measure track conditions at speeds up to 300 km/h without disrupting regular service.
- Stress monitoring systems: Modern rail networks install distributed fiber optic sensing systems along high-speed tracks to continuously monitor rail temperature and stress conditions, allowing real-time adjustments to train operations during extreme weather.
- Mobile stress adjustment units: Advanced rail maintenance trains can now perform on-site stress adjustments using induction heating and hydraulic tensioning without removing the rail from service, dramatically reducing maintenance windows.
- Mobile maintenance factories: Advanced maintenance trains combine multiple operations (grinding, tamping, stabilizing, and measuring) in a single pass, improving efficiency.
- Drone and robot inspections: Many rail networks now deploy drones and autonomous robots for visual and ultrasonic track inspections, reducing the need for human inspectors on active tracks.
Environmental Factors Affecting Track Maintenance
Maglev Train Environmental Considerations
- Temperature variation: Guideway expansion and contraction must be precisely managed, particularly in regions with extreme temperature fluctuations.
- Water and humidity: Drainage systems for maglev guideways must prevent any water accumulation that could affect electronic systems or create ice during freezing conditions.
- Earthquake protection: In seismically active regions like Japan and China, maglev guideways incorporate specialized shock absorption and movement detection systems requiring additional maintenance.
Conventional Track Considerations
- Thermal management: Rail operators globally must constantly balance the risk of rail buckling in summer against rail breaks in winter. Climate change has increased this challenge, with networks implementing more frequent rail stress monitoring and adjustment programs. Learn more here.
- Frost protection: Rail networks in cold regions must manage freeze-thaw cycles that can cause track heave and settlement, requiring specialized drainage and sometimes heating systems.
- Vegetation control: Conventional tracks require regular vegetation management to prevent interference with infrastructure and maintain visibility.
- Flood resilience: Climate change has increased flooding risks, prompting many rail networks to enhance drainage systems and monitoring for washouts.
Regional Adaptation and Challenges
Diverse Climate Considerations
- Desert operations: In regions like the Middle East and parts of China, sand mitigation becomes a primary maintenance concern for both technologies, with maglev systems requiring specialized protection for electronic components.
- Tropical environments: High humidity and rainfall in Southeast Asia and parts of South America create unique challenges for preserving both conventional rail components and maglev electronic systems.
- Arctic conditions: Extremely cold regions require specialized materials and techniques for both technologies, with conventional rail facing challenges from frozen switches and maglev systems needing reliable heating for electronic components.
Cost and Resource Allocation
Maglev Track Economics
- Front-loaded investment: Maglev systems typically require higher initial construction quality but potentially lower ongoing maintenance costs.
- Specialized equipment: Maintenance of maglev guideways requires custom-designed vehicles and tools, representing significant capital investment.
- Extended service life: Properly maintained maglev guideways may have longer service lives than conventional tracks due to the absence of mechanical wear.
Conventional Track Economics
- Continuous reinvestment: Rail networks typically operate on a continuous renewal cycle, with components being replaced at different intervals based on wear patterns.
- Rail stress management costs: Operators allocate substantial resources to rail stress management, with dedicated teams performing seasonal inspections and adjustments. The financial impact of speed restrictions during extreme temperatures (particularly on high-speed lines) can exceed direct maintenance costs.
- Standardized equipment: Conventional track maintenance benefits from standardized equipment available from multiple suppliers, reducing capital costs.
- Labor intensity: Despite increasing automation, conventional track maintenance remains relatively labor-intensive compared to maglev systems.
Can Maglev Trains Overcome the Need for Purpose-Built Tracks?
One of the main challenges facing the widespread adoption of maglev trains is their reliance on specially designed tracks. However, recent innovations suggest there may be a solution. In March 2024, Italian company IronLev conducted a successful test that demonstrated the potential for magnetic levitation technology to work on existing rail infrastructure. The test involved a 1-ton prototype vehicle, which reached speeds of 70 kilometers per hour—without any modifications to the existing tracks.
Looking ahead, IronLev’s next goal is to develop a full-scale vehicle weighing up to 20-tons and capable of reaching speeds of 200 kilometers per hour. If successful, this could mark a significant breakthrough in making maglev technology more accessible and cost-effective.
Conclusion
While Maglev requires less physical maintenance, it relies on specialized equipment and precise alignment which may require advanced solutions. Traditional rail requires intensive maintenance to replace physical components. For future planning, these trade-offs must be considered to accurately calculate the long-term costs.
Conventional tracks benefit from centuries of accumulated knowledge and standardized approaches to maintenance, with well-established procedures and supply chains. The critical practice of rail stressing highlights a unique challenge faced by conventional rail operators that maglev systems avoid entirely. While more maintenance-intensive overall, the mature ecosystem supporting conventional rail maintenance provides resilience and adaptability.