Synchronizing Hydraulic Cylinders: The Benefits of a Pump per Point System

November 1, 2021
0
Synchronizing hydraulic cylinders is essential if you intend to lift a load using multiple lifting points. While this is possible to achieve with an operator and pump at each lift point, it isn’t always the easiest or the safest way to go about it.
Using a synchronized lifting pump provides more accuracy and involves less risk. Pumps of this type work using feedback from sensors and controlling the flow to each cylinder, giving the added advantage of less manual intervention.
Controlled lifting pumps are not a new innovation and are used across a wide range of industries. There are several different options to choose from, and although these all generally do the same thing – each type has varying features to suit the specifics of different lifting applications.
Before we look into the benefits of a pump per point system, let’s take a look and compare the three main types of controlled lifting pumps.
Three Options for Synchronizing Hydraulic Cylinders
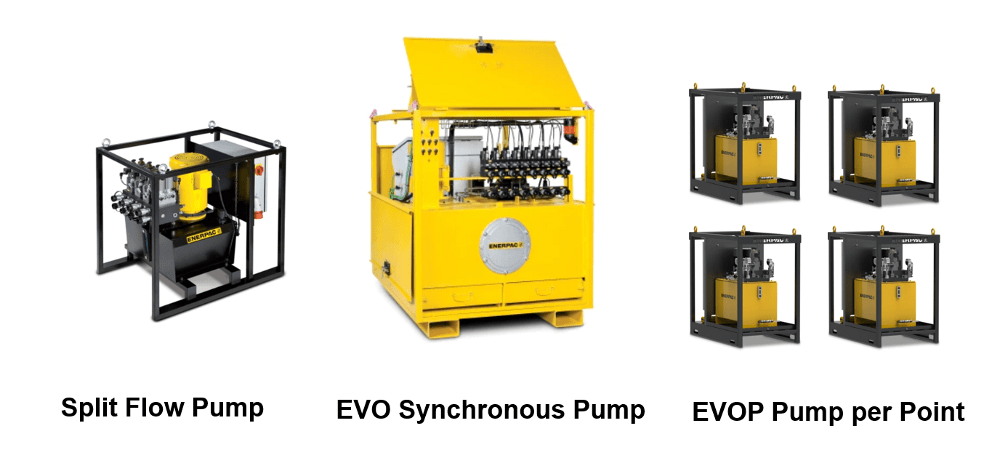
Split Flow Pump
A split flow pump is the simplest type of controlled lifting pump. As the name suggests, the output is split to deliver an equal flow of oil to each cylinder. Simultaneous operation of valves controls the flow to provide an even flow to each lift point. This is done regardless of differences in load. So for an unbalanced load, a split flow pump might not be the optimum solution.
So long as all cylinders have the same load rating (effective area), the stroke of the cylinders will move evenly based on the even output flow. For fine-tuning at each lift point, valves can be controlled individually. Advance / Hold / Retract functions also provide the control needed.
A single split flow pump can be used with up to 8 lifting points and suits lift projects when 4% accuracy between cylinders is acceptable. If more precision is needed, a synchronous pump or pump per point system will be a better choice.
Synchronous Lifting Pump
Synchronous lifting pumps such as the Enerpac EVO Series provide more advanced and specialized functions than a split flow pump. A PLC (Programmable Logic Controller) controls and monitors each lifting point, using feedback from external stroke and pressure sensors. All movements are managed from a central operator station displaying real-time status updates.
Other capabilities include the ability to control the stroke of each lifting point and a controlled tilt function. Precision is greater than a split flow pump, and depending on the cylinders used, an accuracy of 0.040 inches (1 mm) between lift points can be achieved. A single EVO pump can control up to 12 cylinders, and 4 can be used in series to control as many as 48 lift points.
EVOP Pump per Point System
This new system for synchronizing hydraulic cylinders was launched by Enerpac in October 2021. It is designed for multi-point lift applications using high tonnage cylinders, long cylinder strokes, and especially when a fast lift speed is a high priority.
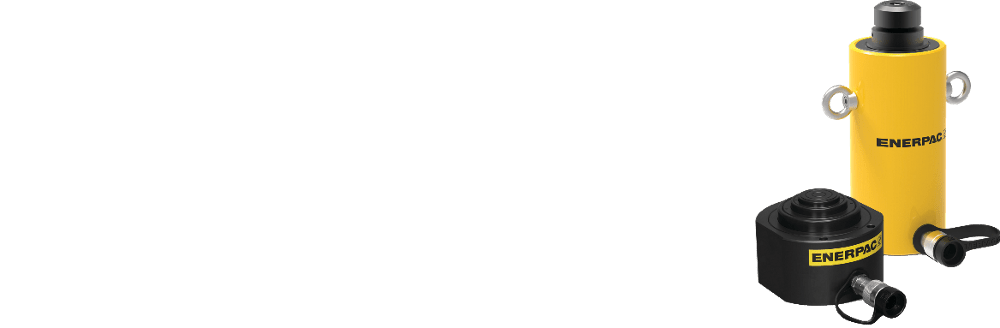
How to Choose the Right Cylinder
The Benefits of a Pump per Point System
- Using a pump at each lift point delivers a high flow rate to each cylinder. This means the lift can be completed faster – without sacrificing precision or safety.
- A two-stage hydraulic pump enables fast retraction. This is very efficient for repetitive operations.
- Ideal for high tonnage cylinders (which need more oil than general-purpose cylinders). The high oil capacity within each pump eliminates the need for custom reservoir designs, which are often needed when using a single centralized pump.
- The VFD motor (Variable Frequency Drive) minimizes starts and stops. This results in a fast lift on long-stroke cylinders, and a smooth lift for sensitive structures.
- The VFD motor speed control also allows flexibility when using multiple cylinder capacities within the same lift.
- As compared to a centralized pump, the reduced distance from the pump to cylinder minimizes hose lengths and the risk of leaks.
- A single pump per point unit can also be used for a standalone operation, providing high flow and pressure for operating other hydraulic tools, using a simple handheld pendant operation.
Application Examples for a Pump per Point System
- Projects needing high tonnage cylinders and/or long cylinder strokes
- Mining equipment maintenance (OEM or aftermarket)
- Climbing jacks (used by construction firms, heavy lifting companies)
- Box jacking/tunnel jacking (by construction firms)
- Concrete pre-stress fabrications
- Bridge launching and skidding
Summary
A pump per point system provides precise synchronization on projects using high tonnage cylinders and long cylinder strokes. The increased oil capacity at each lift point enables fast completion of lift jobs – especially on projects involving repetitive lift and retract operations. Companies that will benefit include those manufacturing or maintaining large vehicles used in the mining industries, and heavy lift contractors. For example:
- Shovel undecking
- Track and wheel maintenance
- Undercarriage repair
Heavy lifting specialists will also find the pump per point system ideal for projects such as:
- Climbing jacks and stage lifting
- Tunnel jacking
- Push/pull jacks for launching or skidding
- Complex and/or sensitive structures or machines
See specifications of Pump per Point Controlled Lifting Pumps (link to product pages)