Precast vs Cast-in-Place Bridges: Advantages and Disadvantages
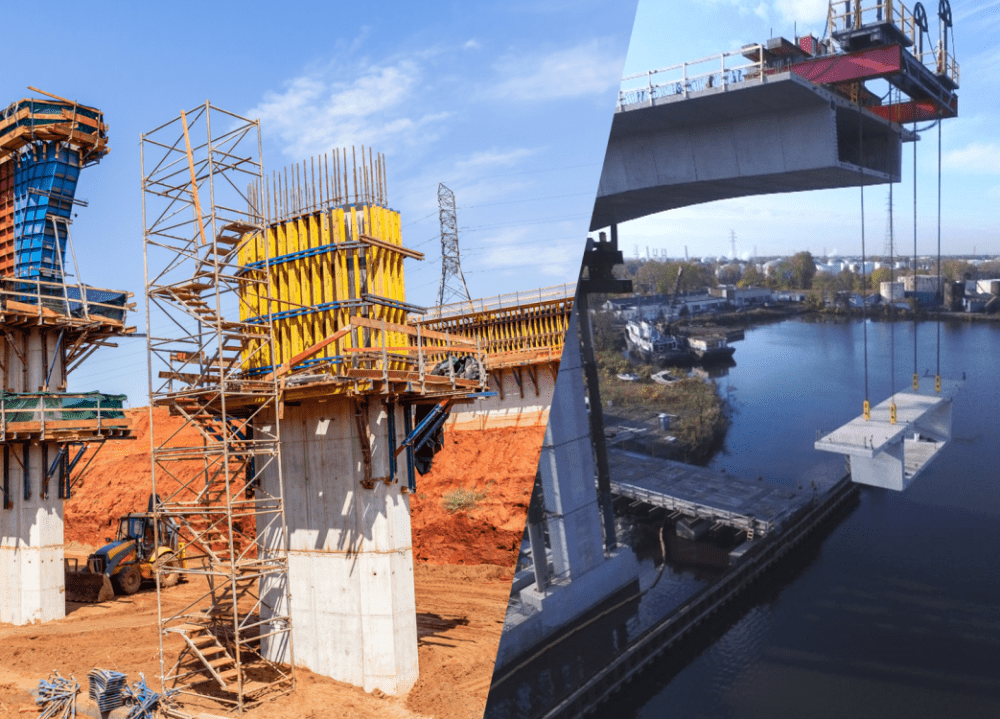
August 27, 2024
0
As engineering and construction technologies advance, the methods for building bridges continue to evolve. When it comes to constructing concrete bridges, two primary methods dominate the industry: precast (prefabricated) and cast-in-place bridges. Each method comes with its own set of advantages and considerations, catering to different project needs and circumstances. In this article, we’ll delve into the differences between precast and cast-in-place, particularly in relation to bridge construction.
Precast Bridge Construction
Precast concrete structures are prefabricated and cured off-site before installation, usually in a manufacturing plant. The process involves manufacturing bridge elements in a controlled environment before transporting them to the bridge site for final assembly. Typical precast bridge components may include concrete beams, deck panels, abutments, piers, and parapets.
Advantages of Precast Bridge Structures
Speed of Construction: Bridges using precast components usually have shorter construction times compared to cast-in-place bridges since much of the work is done off-site. This can result in reduced traffic disruptions and overall project durations. Most precast facilities are indoors and will continue production even during harsh weather conditions.
Quality Control: Fabricating bridge components in a controlled environment allows for stringent quality control measures, resulting in consistently higher-quality end products. Precast manufacturers employ certified technicians and engineers to monitor and aid the team during the production process.
Reduced Site Disruption: Prefabricated construction minimizes on-site work, reducing noise, traffic congestion, and environmental disturbances.
Enhanced Safety: With less on-site activity and a smaller workforce there’s potential for improved safety of workers and others in the surrounding area.
Aesthetics: Manufacturing precast concrete components in a controlled factory environment allows the potential to use different combinations of colors and textures, including more visually pleasing smooth finishes.
Disadvantages of Precast Bridge Structures
Transportation Challenges: Transporting large bridge components to the site can pose logistical challenges, especially for oversized or overweight elements, requiring specialized heavy-lifting equipment and careful planning.
Limited Design Flexibility: Bridges that use multiple precast parts with the same specifications can have limitations in terms of design flexibility, whereas cast-in-place construction offers the capability to create irregularly shaped, unique, and complex structures.
Initial Cost: Precast bridges may have higher upfront costs due to the need for specialized manufacturing facilities and transportation logistics. Many projects and precast components are needed to ensure sufficient profit from the initial investment.
Example Using Precast Components
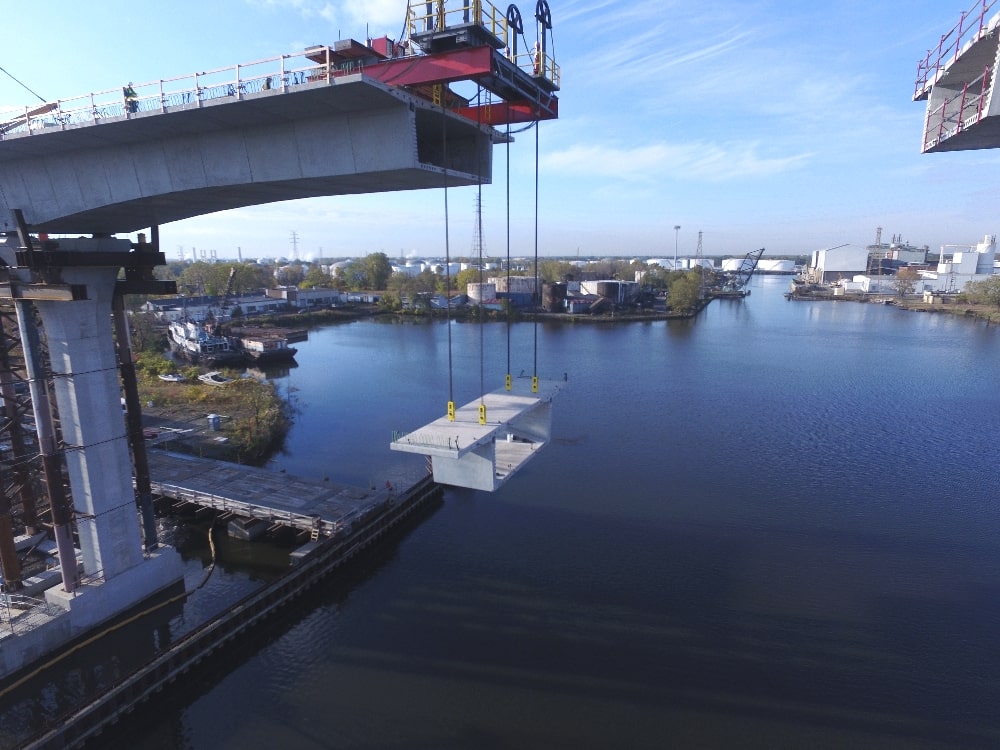
Cline Avenue Bridge in East Chicago: An elevated expressway based on the balanced cantilever method using precast segments. It was built using a mix of traditional and new techniques. Enerpac Strand Jacks were used to lift precast deck sections from a barge below. Learn more in this article
Cast-in-Place Bridges
Cast-in-place may be regarded as the more traditional construction approach for concrete structures. This method involves pouring concrete directly into formwork on-site (also known as falsework), allowing for greater flexibility in design and construction.
The components may be cast in position, or alongside the final location and lifted or slid to place using specialist heavy-lifting equipment. Typical bridge components cast-in-place can include foundations, walls, footings, caissons, piers, pylons, columns, road decks, slabs, and beams.
Advantages of Cast-In-Place
Design Flexibility: Cast-in-place construction offers flexibility in terms of bridge geometry, allowing for custom designs tailored to specific site conditions and project requirements.
Less Transportation Requirements: Since the components are built on-site, there are fewer transportation challenges as compared with precast bridge sections.
Cost-Effectiveness: Cast-in-place construction can offer long-term cost savings. The durability and adaptability of cast-in-place structures result in lower maintenance and repair expenses over their lifespan.
Durability: The simpler and often monolithic structure of cast-in-place bridge sections involves less joints than those encountered with the precast method. This reduces the risk of joint deterioration and as a result ensures long-term structural integrity, particularly in high-traffic areas or areas prone to earthquakes.
Adaptability to Site Conditions: Casting concrete on site allows for real-time adjustments to account for the unexpected, such as ground conditions or environmental factors.
Disadvantages of Cast-In-Place
Longer Construction Time: Due to the on-site casting and curing processes, cast-in-place construction typically requires more time than precast methods. Additionally, unfavorable weather can cause delays to the schedule.
Quality Control Challenges: Ensuring consistent quality may be more challenging with on-site precast construction, as environmental factors and site conditions vary and can impact the curing and setting of concrete.
Site Disruptions: Compared to prefabricated construction, cast-in-place activities can cause more lengthy disruption to traffic and nearby residents. More labor is required for both creating formwork and throughout the casting stage.
Example of Cast-In-Place Bridge Components
Millau Viaduct in France: The Millau viaduct holds the world record for the tallest bridge at 343 m high (1125 ft) which is higher than the Eiffel Tower. The seven concrete pylons were built in place, the tallest being a colossal 245 m high (803 ft).
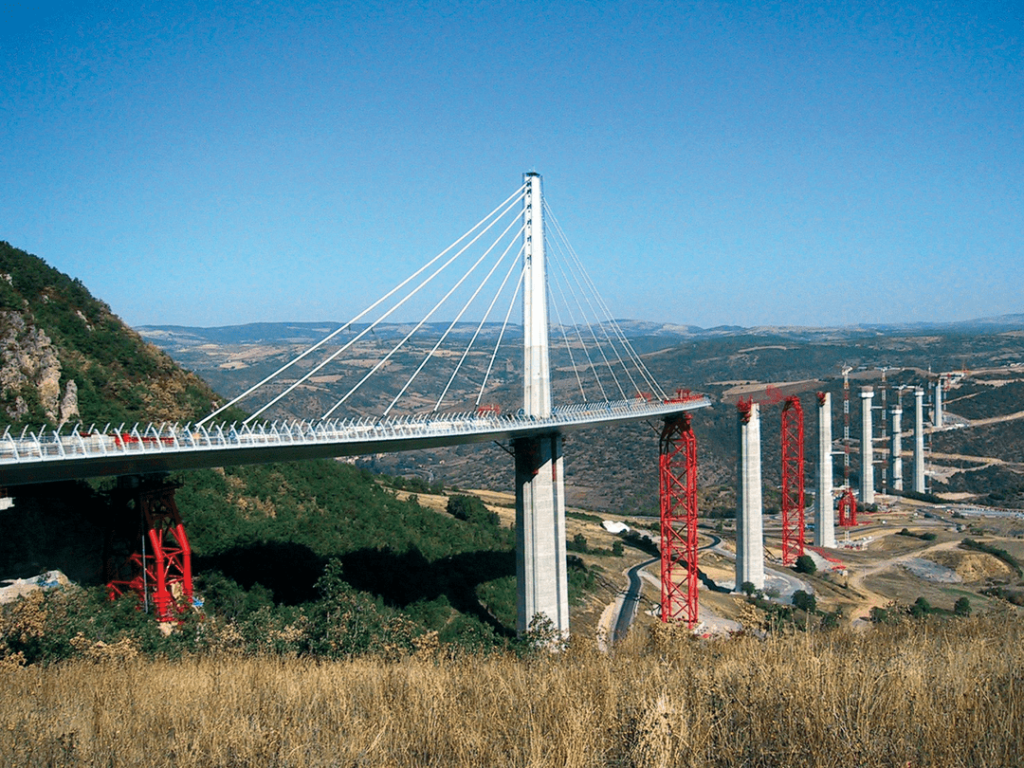
Equipment for Lifting, Transporting, and Installing Bridge Components

Transporting and positioning precast bridge components presents unique challenges. In many cases a crane may not be suitable because of access difficulties, or if precise control is needed. Some excellent alternatives to cranes include:
Strand Jacks: Equipped with high-tensile steel cables, and commonly used for lifting heavy prefabricated bridge segments. These hydraulic lifting systems work from a small footprint and offer precise control, enabling contractors to raise position components accurately.
Jack-Up Systems: Provide temporary support for prefabricated bridge segments during installation. These systems often use four jack-up units that build lifting towers from high-strength steel barrels. They can be mounted on the ground or onto a Self-Propelled Modular Transporter (SPMT).
Self-Propelled Modular Transporters (SPMTs): These are instrumental in transporting oversized prefabricated bridge components from manufacturing facilities to construction sites. These modular transporters feature hydraulic suspension systems, allowing for smooth and controlled movement of heavy loads.
Lateral Sliding Systems: During bridge construction and replacement, minimizing the disruption caused by road and waterway closures is essential, which is why there is a shift towards ‘accelerated bridge construction’ methods (ABC). An example of this is sliding a new bridge deck into place with a system that includes Enerpac hydraulic jacks, hydraulic pumps, a toothed track, and low-friction Teflon plates.
Synchronous Hoist: The Synchronous Hoist System is not an alternative to a crane, it serves as an enhancement to provide more precision. The Enerpac system is below-the-hook sling adjuster which typically includes multiple specialized hydraulic cylinders mounted directly in-line with the rigging. It gives the operator the freedom to precisely monitor and adjust each lifting point independently – especially useful for positioning heavy and unbalanced loads.
Summary
Both precast and cast-in-place bridge construction methods offer distinct advantages and disadvantages. The choice between them depends on project-specific factors such as budget, timeline, site conditions, and design requirements.
While precast bridges excel in speed, quality control, and reduced site disruption, cast-in-place construction offers greater design flexibility, adaptability to site conditions, and potentially lower initial costs. Ultimately, engineers and contractors must carefully evaluate these factors to determine the most suitable construction method for each bridge project.
For many projects it doesn’t have to be just one or the other. Throughout the world it is becoming more common to specify bridges that rely on both methods. In Europe this is known as hybrid concrete construction (HCC). In the United States, the Federal Highway Administration (FHWA) doesn’t use the term “hybrid,” but encourages transportation departments to use structural precast bridge elements and systems (PBES) where possible, to minimize disruption.
If you have a bridge project in mind and want to discuss equipment options, contact your nearest Enerpac Heavy Lifting Technology specialist.