Pneumatic vs Hydraulic: Which Torque Wrench Is Right for You?
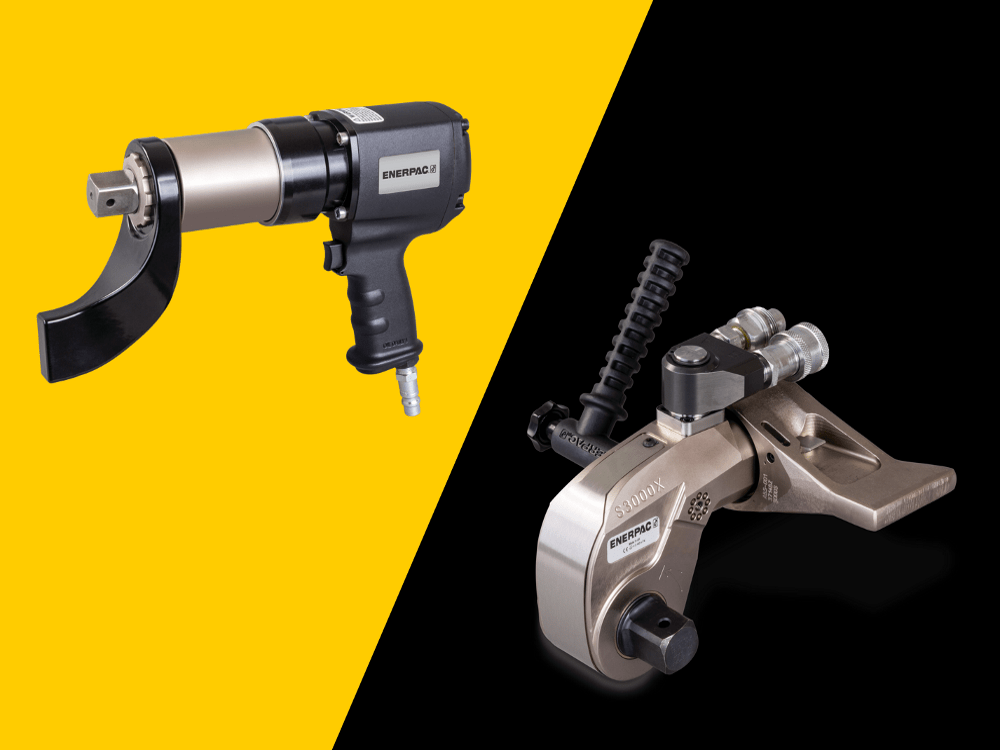
March 15, 2022
0
Considering pneumatic vs hydraulic is arguably the most fundamental decision to make when choosing your next high-capacity torque wrench. Experienced bolting technicians will be well aware of the pros and cons of each, but if you’re new to this area, or buying on behalf of a colleague, it’s worth taking the time to make sure you understand the key differences.
So, which is best? Unsurprisingly, the simple and short answer is that it depends on the intended applications. Let’s take a look at some of the key areas and compare both types.
Location
If you will be working inside a factory where a compressed airline isn’t available, simply put, a pneumatic torque wrench isn’t a viable option. When working at remote locations, such as on pipelines and outdoors at refineries then a hydraulic wrench offers more portability.
Torque Output
For high torque applications on large fasteners, hydraulic tools come out on top. When you compare similar-sized torque wrenches, a hydraulic torque wrench can be more than 6 times more powerful than its similar-sized pneumatic equivalent. The maximum torque capacity of a large hydraulic torque wrench can be as much as 35,000 ft.lbs (47,453 Nm).
Speed
For high-cycle applications, fast tools are essential to maintain optimum productivity. For this type of work, a pneumatic torque wrench will outperform a hydraulic wrench. This is why they’re favored for product assembly applications, such as on automotive production lines. They offer high-speed continuous rotation and feature a low friction planetary gearbox to minimize wear and extend uptime.
Convenience and Ease of Use
Pneumatic torque wrenches are generally less complex than hydraulic equivalents. As a result, operators find them easier to use. They’re powered by an airline which means there’s no need for a hydraulic pump, specialized oil, and all of the associated extra maintenance. They are commonly used by a single operator – unlike hydraulic when often an extra technician may be needed to handle the controls at the hydraulic pump or pendant.
Pneumatic vs Hydraulic: The Safety Considerations
Using both types of these powerful tools exposes operators to the risk of injuries to the hand. But aside from pinch points, there are other safety pros and cons to weigh up.
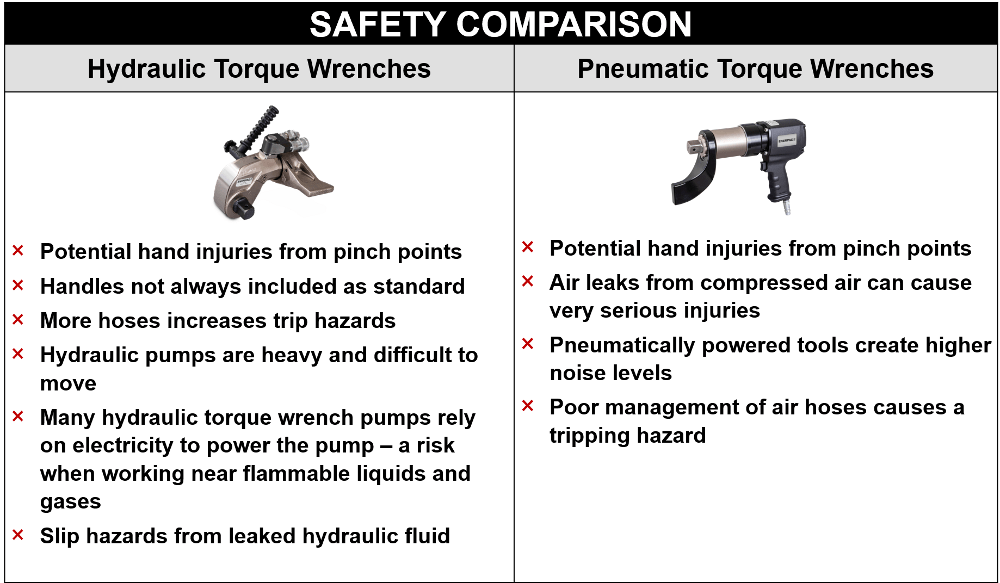
Accuracy
On average, a pneumatic torque wrench provides an accuracy of +/- 5%. This is generally accurate enough for most assembly work. Hydraulic torque wrenches provide greater accuracy – typically +/- 3%.
Cost
So long as a compressed air line already exists, pneumatic torque wrenches are an economical choice. You don’t need a separate pump as they rely on an infinite power source (air) – just connect the torque wrench and filter to the airline and you’re good to go!
Pneumatic vs Hydraulic Comparison Table
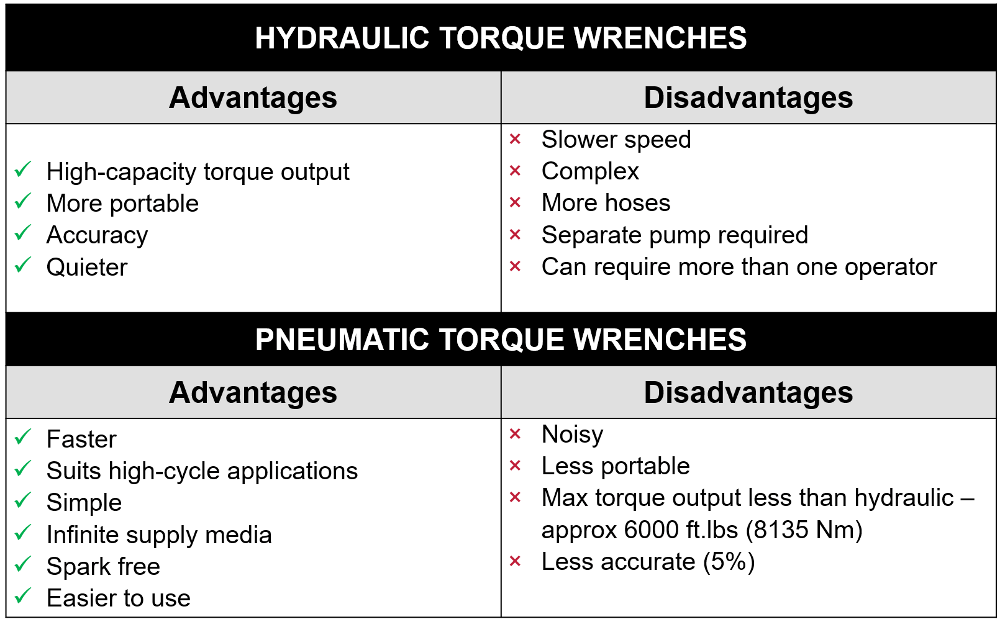
Conclusion
Both hydraulic and pneumatic torque wrenches are excellent tools when used for the right applications. The major considerations are the torque output needed, where the tools will be used, and whether the work is high-cycle.
If you’re going to be working outside at a power plant, pipeline, or refinery, then a hydraulic torque wrench is most likely to be the right tool – especially if the work will involve large fasteners. If working in a factory environment on high cycle applications, then pneumatic is likely to be the better choice.
In either case, you can find full specifications of hydraulic and pneumatic torque wrenches on the main Enerpac website.