Overcoming Pin Removal Challenges in Heavy Equipment and Plant Machinery
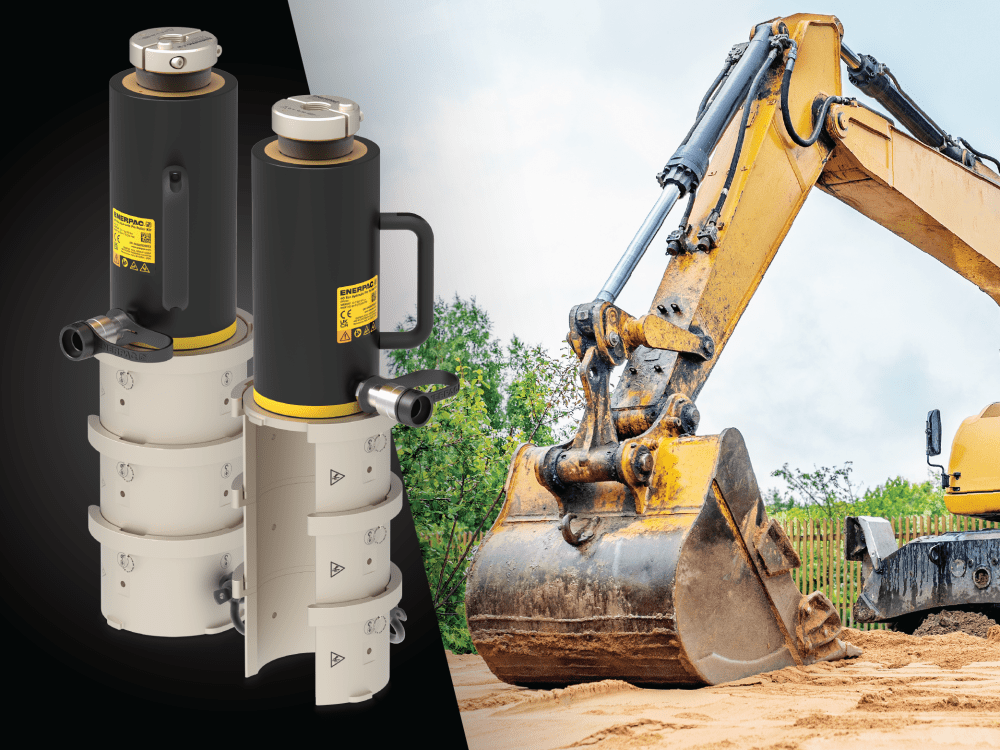
July 25, 2024
0
Industrial pins are an essential aspect of heavy equipment vehicles and plant machinery, offering much-needed flexibility for maintenance and operation. They are simple and effective, designed to fit tightly into their corresponding holes, and are often held in place by the friction and interference fit or by other securing methods.
This is all very helpful – until it comes time to extract the pin.
Pin pulling is a vital maintenance activity. Pins are intended to be removable, allowing operators to remove parts for maintenance, change attachments, (such as buckets on a backhoe), or partially dismantle plant equipment for transportation, like the folding boom on a crane.
But if a pin cannot be removed, on-site operations will quickly be affected.
What Causes Pin-Pulling Problems?
Even in the best-maintained system, pin removal will require significant force, purely because of the close fit of the parts.
Hardware design
The snug fit of industrial pins ensures they do not work loose when equipment is in use. Should a pin fall out accidentally, the damage could be catastrophic – which is why they are extremely tight-fitting. Unfortunately, that can make pin removal quite difficult.
Environmental factors
In certain environments pins may be subject to severe corrosion or contamination, making them harder to remove. Similarly, pins exposed to very high or low temperatures can affect the materials and the tools used, potentially complicating the pin-pulling process.
Accessibility
Pins are often located in hard-to-reach areas, making it difficult to remove pins manually. This is especially common in complex machinery and compact assemblies where surrounding components might obstruct access to the pins.
The problems with manual pin pulling
Traditionally, pins would be pulled manually. Simply striking the pin with a large hammer (often repeatedly) would be enough to force the pin from its mounting. Where pins become stuck, applying direct heat should cause the pin to contract slightly – hopefully enough to get the pin moving again. Other approaches include welding threaded bolts to the pin, using the pecker fitting on a mini digger or even using a jackhammer to deliver vibration and force directly onto the head of the pin.
In theory, all of these approaches could work – but there are some significant drawbacks.
Health & Safety Considerations
There is always an element of risk attached to swinging large, heavy hammers. Any worker involved in manual pin pulling is at risk of hurting themselves when striking pins, particularly as the activity is extremely high impact. The worker may strike themselves or others with the hammer or injure themselves through repetitive actions.
The risk increases exponentially when torching or lancing the pin.
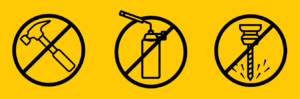
Force and precision
Heavy hammers are never used for high-precision activities on site – but striking a pin correctly is a precision activity. Manual pin pulling requires a precise degree of force to be applied to a specific point on the pin. This can be extremely hard to achieve when a stuck pin requires hundreds of identical precise blows.
Potential equipment damage
Strike the pin wrong and you could damage it, further complicating the removal process. Worse still, other parts of the equipment or plant machinery could be damaged by a poorly aimed blow or using unrecommended tools like a jackhammer. Repairing the damage could be extremely costly.
Wasted time and resources
There are plenty of online stories about how manual pin removal requires several people over a period of hours, especially when dealing with seized pins. That’s time employees could be spending on other more important tasks. Every wasted man-hour eats into the profitability of your on-site operations – and could delay other important project tasks.
How to Extract Pins Properly: The Enerpac PPH-Series
Using a dedicated pin puller can help to mitigate these risks. Units like the Enerpac PPH40 and PPH60 Pin Pullers are specifically designed to overcome the day-to-day challenges of pin pulling.
Improved Pin Pulling Safety
Dedicated hydraulic pin pullers provide huge amounts of pressure required to ‘unstick’ pins from equipment – no additional heating required. Because with that power, if precisely directed, the risk of injury during pin pulling is dramatically reduced.
Faster and more efficient
The Enerpac PPH-Series Pin Pullers can be operated by a single operator. The removal process should take a matter of minutes, requiring just one person to fit the puller and monitor its progress – even when dealing with stubborn, seized pins. This means that the rest of your team can focus on more productive activities.
Controlled power
The pin-pulling tool can be controlled to ensure that just the right amount of force is applied to the pin. By controlling power and direction, the operator ensures that surrounding equipment, and the pin itself, is not damaged. A selection of add-on quick nuts provide additional interfacing and removal options if required.
What about on-site challenges?
Despite generating huge amounts of directed pressure, pin-pulling tools are not necessarily large. The Enerpac PPH40 pin puller creates 40 tons of pressure but is relatively compact and weighs just 50 pounds. The unit can be powered by electric, air or cordless pumps, offering maximum flexibility on site and allowing pins to be pulled anywhere.
Work smarter
Manual pin pulling should work – eventually. However, in many cases the physical risks to health, safety and equipment cannot be fully justified – particularly when there are powerful, low-contact alternatives available that can complete the job faster and more safely.
Using a specialized pin pulling tool is faster, more effective and has far fewer risks than hoping ‘heat and a hammer’ will get the job done.
To learn more about smart pin pulling and how to solve pin pulling headaches, take a look at the Enerpac Pin Puller range.