What are Spiral Wound Gaskets?
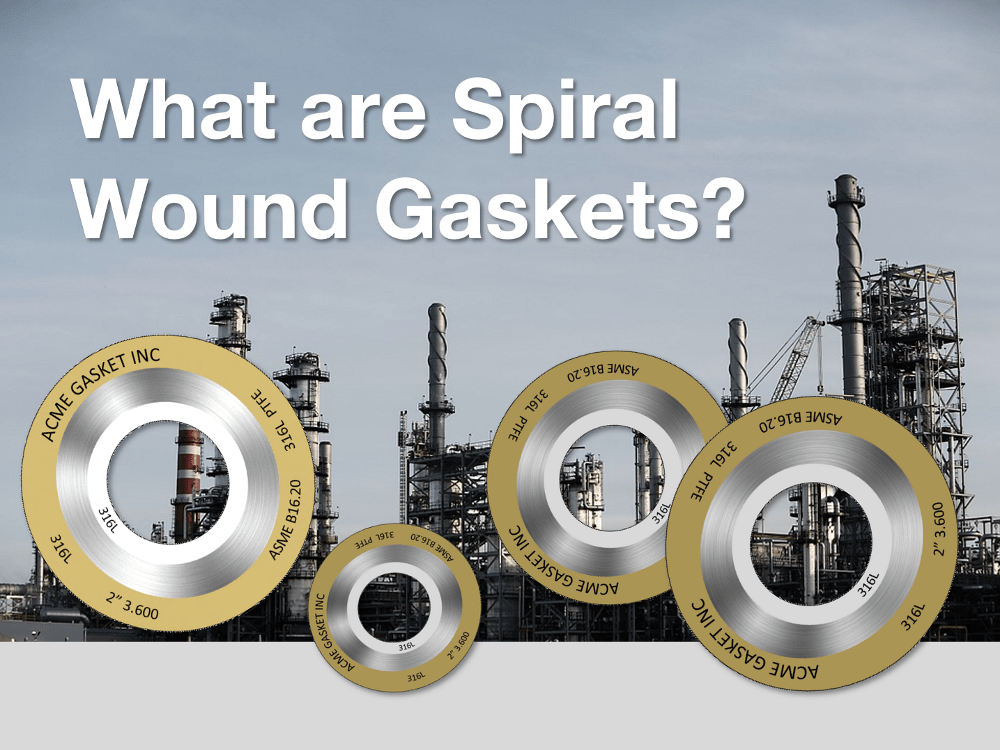
June 11, 2018
0
The spiral wound gasket was developed in the early 20th century to meet the increasingly demanding conditions encountered in oil refinery operations. This type of gasket is commonly used with flange surface finishes created using a flange facing machine, which is why we decided to put together this simple overview as an introductory guide for the on-site machinist.
Gaskets used in the oil, gas, and petrochemical industries need to be engineered to cope with high pressures, extreme temperatures, and chemical attack. Fluctuations in the above, along with temperature differential across the flange face and bolt stress relaxation, demand a gasket with flexibility and recovery. The need for the gasket to recover from changing conditions cannot be overemphasized.
Gasket Construction
The spiral wound gasket is semi-metallic, comprising of a spirally wound v-shaped stainless steel strip and a non-metallic filler material, such as graphite or PTFE. Also on the gasket, is a solid outer ring used for centering and controlling compression. This minimizes the risk of material creep through over-tightening.
For the toughest conditions, spiral wound gaskets are available with an additional inner ring. This protects the windings (particularly the filler), from contamination, or attack by the product travelling past the pipeline joint.
Material Combinations Used in a Spiral Wound Gasket
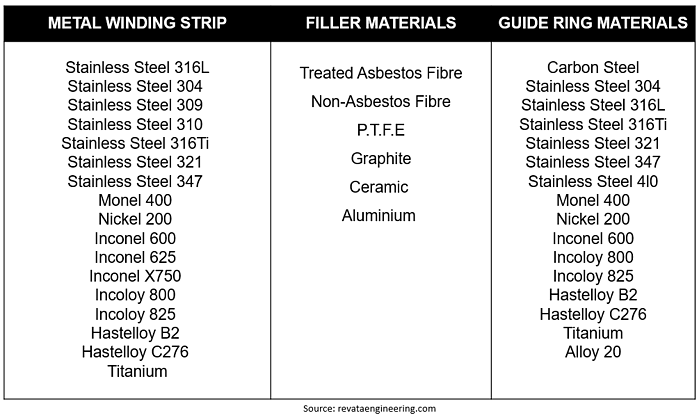
Industry standards require that gaskets are color-coded. This is to identify metal and filler materials listed in the ASME B16.20 regulations. The image below shows the required markings for compliance.
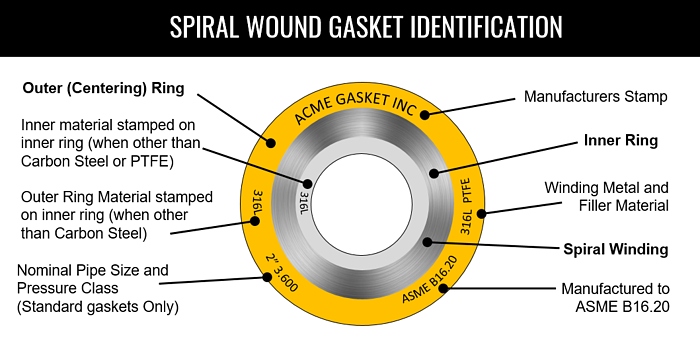
Using gaskets made by manufacturer ‘Flexitallic’ as a representative example; the image of stacked gaskets below shows how the outer edge ring colour denotes the metallic winding material (Top row), and the filler material by coloured stripes around the gasket edge at equal intervals (bottom row).
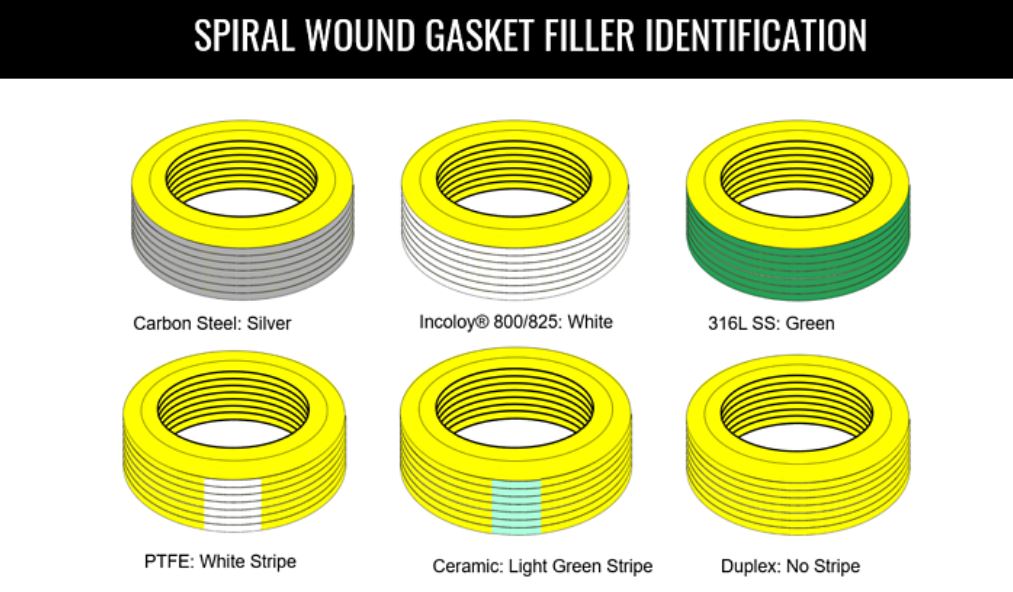
Installation of Spiral Wound Gaskets
Disclaimer: The list below is just a basic overview and should not be taken as formal advice or instructions. Please consult with your gasket manufacturer.
- When installing gaskets onto a new flange, or if replacing an old one, the flange faces should be clean and free from indentations and scoring. Cross-face scoring is a major concern as this can lead to joint leakage.
- When scoring is present, the flange surface can be re-machined using a portable machine tool such as a Mirage Flange Facing Machine.
- Gasket manufacturer ‘Flexitallic’ recommend a surface finish of between 3.2 µ to 6.3µ. A surface comparator is a useful tool used to check the finish.
- The flange faces should be parallel and be concentric, without the need for pulling them into position with excessive bolt loads.
- A spiral wound gasket should never be re-used. Always use a new one.
- Before installation, check the gasket is not damaged and that it meets the required correct specification.
- Jointing compounds or lubricants should not be used.
- After installation, check the flange faces are parallel. This can be carried out with a flange gap measurement tool.
Find out more about flange facing machines here. If you would like to speak to your regional technical sales representative get in touch here