Key Considerations for Choosing a Workholding Pump
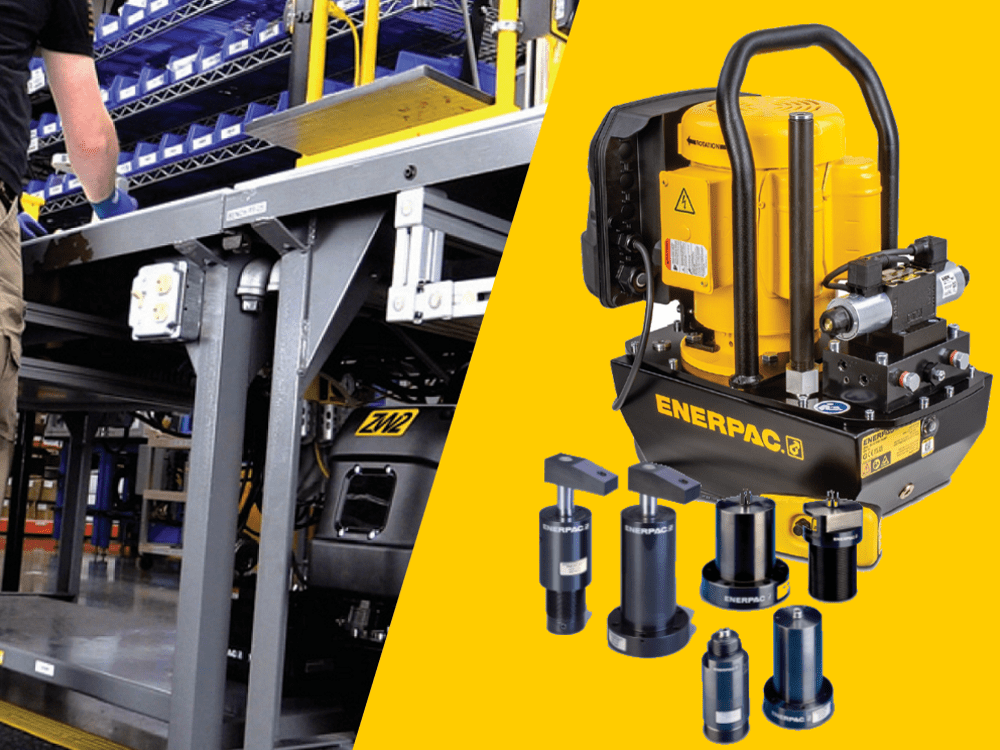
August 24, 2021
0
Before we look at choosing a workholding pump, first, let’s remind ourselves what powered workholding is, and the benefits it brings to manufacturers.
Workholding Basics
Workholding uses powered systems to position, support, and clamp parts during manufacturing. Compared to more manual methods, powered workholding tools deliver huge productivity increases – especially during machining, punching, pressing, and other operations. Using this approach reduces setup time, delivers consistent results, improves safety, and results in fewer scrapped parts.
A hydraulic system for workholding is made up of cylinders, pumps, valves, and other components that control and automate the process. Your choice of workholding pump has huge implications on what you can and can’t do. So, it is worthwhile doing your homework and working through the key considerations.
Hydraulic vs Pneumatic Systems
Workholding systems can be powered hydraulically – using a pump, or pneumatically – using the airline within the factory.
Pneumatic workholding uses compressed gas clamps (usually air) to achieve their gripping force. The drawback is the size of cylinder needed to generate the required holding forces, and the volume air itself which will compress. This is why pneumatic workholding systems are more suited to smaller workpieces.
Hydraulic workholding creates a more powerful gripping force by using power from applying pressure to hydraulic oil (which, unlike air, does not compress). This is faster, more powerful, and better for use with larger workpieces.
The Benefits of an Electric Hydraulic Pump for Workholding
Hydraulic pumps are available in many different power configurations. But for workholding purposes, the electric motor driven type is the clear winner.
Although priced higher than other pump types, they offer the greatest flexibility and output capacity. They deliver the highest flow rates and are the preferred choice for large circuits with high duty requirements. An additional benefit is they can be configured with many different options.
Workholding Pump Flow Rates
Hydraulic pumps are available with different flow rates. Typical examples such as the Enerpac ZE2 and ZW2 pumps vary from 20 to 40 in3 /min at rated pressure. Therefore, planning your system in advance and calculating the required flow rate is essential.
Noise Level
Manufacturing plants are usually noisy places to work. So anything that helps keep the noise levels to a minimum is welcome. Hydraulic pumps designed for workholding applications take this into account. You can expect the noise level to be within 71 to 79 decibels. To put this into perspective, this is similar to a vacuum cleaner, less than city traffic, and below the threshold at which sustained exposure may result in hearing loss.
Risk of Overheating
If your pump is to be used continuously, it is important to select a model that will not overheat. Heat is generated from the friction encountered by moving parts – so using a pump with heavy-duty bearings will help extend its life by reducing heat, improving lubrication, and reducing wear.
Versatility of Your Workholding Pump
The key is to understand exactly what you want your workholding system to do – not just from the outset, but also when looking further ahead.
- Multiple valve and control options provide the flexibility to match the pump to a wide range of applications.
- Consider if you need advance, hold, and retract functions.
- Will you be using single-acting or double-acting devices?
- If you need a solenoid dump valve, these can be specified too.
- Choose between pendant or manual controls.
Durability
Shopping around for the cheapest pump may seem attractive to some buyers. But choosing a workholding pump from a trusted brand will help to keep your production line working for longer without too many costly interruptions.
Consider the environment where the pump will be located and if the exterior of the pump will protect the electronics and other internal components. The pump should be IP54 rated – (IP stands for “Ingress Protection”). An IP54 rating means your product will be protected against contamination from limited amounts of dust and other particles.
Protect your pump from unwanted movement by selecting a model that can be fixed to a workbench or other structure.
Maintaining Your Workholding Pump
Through continuous use for extended periods of time, even the most durable pump will need maintenance. If the piston check valves are the kind that can be replaced this will increase the service life of major pump components.
Important System Components
There are many different components you could use within your workholding system – (too many to list here). Three of the most important are…
Pressure Gauges
These are your “window” to the hydraulic system, revealing the status of various parts of the hydraulic circuit.
Filters
Filtering is a must! Contaminated hydraulic oil is widely regarded as the number one cause of failures. Filters can be installed in the high-pressure line, return line, or both.
Fluid Lines
These can be steel tubing or hose. Care should be taken to use only the specified tubing, hose, and fittings in order to assure reliable and safe operation.
Hydraulic Oil
This is the lifeblood of the workholding system and shouldn’t be taken for granted. A manufacturer-specified oil has controlled characteristics, such as viscosity, flash point, and pour point.
Summary
The key considerations for choosing a workholding pump are listed below.
- Hydraulic Vs Pneumatic
- Benefits of Electric Powered Pumps
- Flow Rate
- Noise Level
- Versatility
- Durability
- Maintenance
- Pump Accessories
In summary, an electric motor-driven hydraulic pump is a great choice for a workholding system. Recommended models are the ZE2-Series and ZW2-Series pumps.
See the full range of Enerpac Workholding Tools.