Machinability Rating and Chart Download
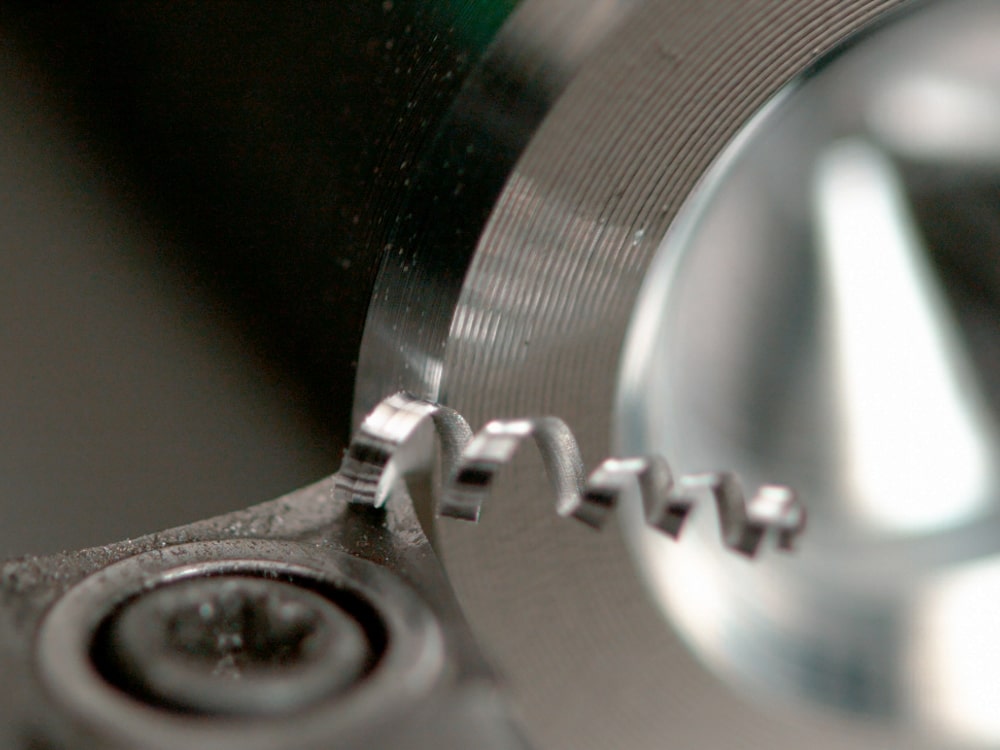
February 1, 2021
0
Each portable machine tool in our Mirage product line is designed with ‘machinability’ in mind. But what exactly is machinability rating and how is it measured?
Definition of machinability
The machinability rating of a material is the ease with which it can be cut by a tool to achieve the required finish. A material that is easy to machine requires less power, takes less time to cut, and will not wear the tooling quickly. The outcome of this is a good surface finish.
Manufacturers of metal components face the challenge of balancing machinability with performance. Typically, the easier a component is to machine the less ‘performance’ it delivers.
By performance, in this instance, we mean strength and durability.
Materials and their effect on machinability
The properties of a material that impact its machinability include:,
- Thermal conductivity
- Modulus of elasticity
- Thermal expansion
- Tensile strength
- Work hardening
Crystal structure and chemical composition
The crystal structure and arrangement of atoms within the crystal grains and their boundaries has a significant impact on the ease of material removal.
Heat treatment, work-hardening and fabrication change the crystal structure, making the metal more difficult to machine.
Chemical composition also changes machinability, for example adding carbon increases the strength but makes the metal more difficult to machine.
Other factors influencing machinability rating
Tool Geometry
The design of the tool has a major influence on machining. The angle of the rake face, clearance faces, and ‘chip breaker’ each play their part in creating a trouble-free and clean cut. You can find out more about this subject in our previous blog post Understanding Cutting Tool Geometry.
Tool Material
Selecting a cutting tool with correct hardness for the material. Toughness and wear resistance are the key factors. High-speed steel is available in M and T types (Molybdenum and Tungsten) and provides better performance than carbon steel. Tungsten Carbide tool bits are an alternative which last longer, but these are more brittle.
Speeds
The cutting speed is the most important factor for extending tool life. The cutting speed must be set to suit the machinability of the material. A high cutting speed may produce a good finish at first, but this is at the expense of excessive tool wear – making it difficult to maintain the correct dimensions.
Feed Rate
This is the speed at which the material is fed into the tool. In the case of drilling this means how fast the operator or auto-feed is pushing a drill bit into the job.
Depth of cut
The depth of cut refers to the amount of material in contact with the tool. For example, the depth of cut set on a milling machine using the Z-axis on the spindle.
Rigidity of the machine
Even if everything else correct, a machine that is not stable will produce poor results.
Machine design factors that can affect accuracy include;
- Ball screw drives
- Spindle power
- Quality of the bearings
- The clamping design
- The overall weight and robustness of the machine
How is machinability rating measured?
The American Iron and Steel Institute (AISI) carried out turning tests on many metals at 180 surface feet per minute (sfpm). The weighted averages of normal cutting speed, surface finish and tool life were then determined for each material.
The metal 160 Brinell B1112 steel was set as the 100% reference point and used to compare the machinability rating of other metals. Metals with a value of more than 100% are softer, and therefore easier to machine. Those less than 100% are harder materials and more difficult to machine.
This method provides a useful reference point as an approximate guide, particularly for turning. If the exercise was repeated using machining types other than turning, the results may throw up some inconsistencies.
Metal Machinability Rating Chart
Download a PDF version of the Machinability Rating Chart like the one below.
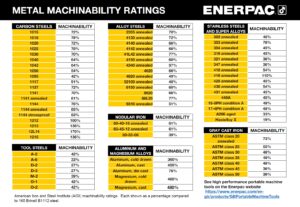