In-Situ Machining: Have You Got What It Takes?
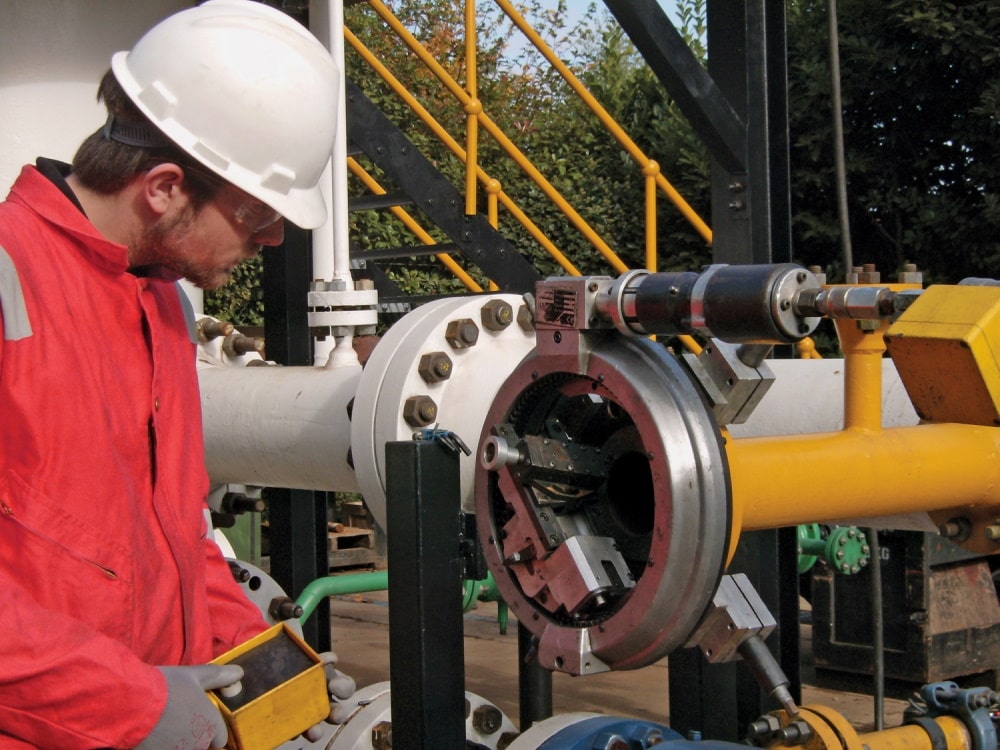
July 12, 2022
0
• The Role of an In-Situ Machinist
• Projects and Activities
• The Right Equipment
• Work Pattern
• Personal Characteristics
• Entry Requirements
The Role of an In-Situ Machinist
An in-situ machinist, also known as an on-site machinist, or field machinist, does much of their work on the customer’s premises. The activities of these unsung heroes keep processing plants, oil and gas installations, and power stations operational, efficient, and safe.
The role is very different from a machinist in a manufacturing facility. While there is some crossover of skills and knowledge, the onsite machinist must be ready to travel at short notice, solve problems, and have the flexibility to cope with challenging work patterns.
Typical In-Situ Machining Projects
Many onsite machining projects center around pipework, especially on flanges and connections to valves, pumps, and vessels. Day-to-day examples are listed below.
• Machining a spiral serrated finish on flange surfaces. Including pipe flanges and heat exchanger flanges.
• Adding new tie-ins (connections) to pipework.
• Pipe cutting and bevelling – often during construction of a refinery, LNG terminal, or a petrochemicals plant. Bevelling and other end pipe-end treatments are done as preparation before welding a flange onto the pipe.
• At a refinery, onsite equipment such as pumps and motors are mounted onto skids or metal pads. For this equipment to function efficiently, the metal mounting pads need to be machined perfectly flat to avoid unnecessary vibration stresses.
• Heat exchangers are common at industrial installations, and after a while can become corroded. Refurbishing these includes machining connecting flanges and division slots at the end of the heat exchanger.
• Machining large cylindrical parts, such as shafts and other rotating turbine components – with a Journal turning machine or line borer.
• Removing flange studs and re-threading.
• Machining large diameters, such as crane pedestal faces.
• A wide range of drilling applications using heavy-duty drilling machines.
• Offshore decommissioning – cutting through caissons, casings, and subsea pipes
The Right Equipment
Aside from the experience, knowledge, and skill of the operator, using quality portable machine tools can make a huge difference. Choose from a reputable manufacturer and your equipment will keep delivering the accuracy and efficiency needed for many years. Cheap equivalents should be avoided. While they may look shiny and new on a website, the reality is they may be difficult to set up, have a flimsy construction, and deliver poor results.
Typical machine tools with links are listed below.
Flange Facers Portable Milling Machines Clamshell Cutters Decommissioning Drilling Machines Portable CNC Mill Orbital Milling Machines Hot Tapping and Line Stop Machines
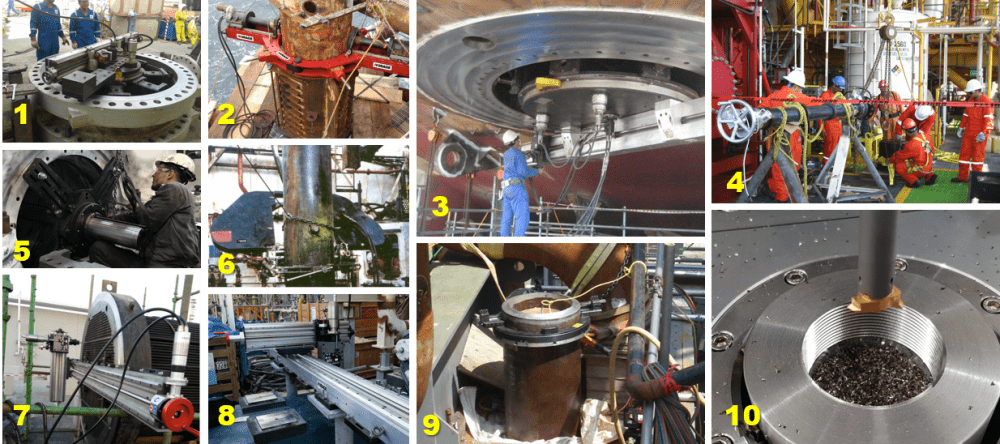
Work Pattern
A typical in-situ machinist will spend most time out in the field, on an industrial site. However, some work can be done back in the workshop, such as small machining jobs, maintaining machine tools, and project paperwork.
If you enjoy travel and don’t mind being away from home this job will suit you. One day you could be working in a refinery in India, the next day you could be on your way to a job in the Middle East. A typical assignment requires availability at short notice, and this could last from a single day to a couple of weeks.
If you like a traditional 9 to 5 work pattern, this isn’t the ideal vocation for you. An In-situ machinist may be required to work anti-social night shift and back shift spells to get vital jobs completed on schedule. Overtime at short notice is also common.
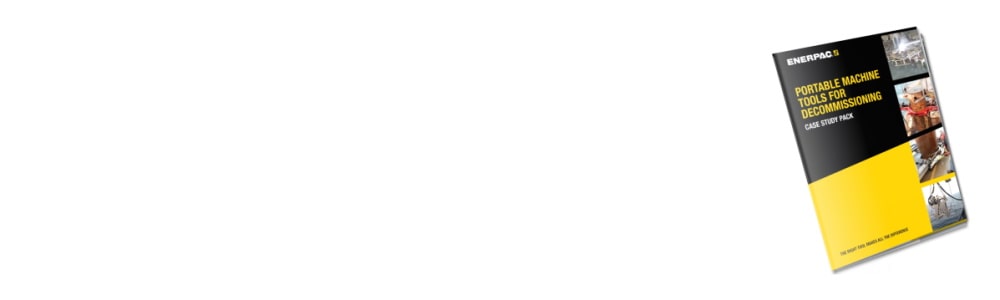
Decommissioning Case Study Pack
Learn how portable machine tools solved four tough decommissioning challenges
Personal Characteristics
An in-situ machinist may work on projects big and small, and in varying team sizes – so good interpersonal communication skills are essential (written, spoken, and reading). An understanding and respect for all cultures is also important.
The critical nature of the work means you need to handle working under pressure, and this may be in harsh environments, tight spaces, and at height. Physical fitness is also important. You should be comfortable meeting productivity goals – but not at the expense of quality and safety.
Entry Requirements to be an On-Site Machinist
Apart from the personal qualities, there are some prerequisites needed to get you into this vocation.
Education and Qualifications
A typical entry-level job description will usually expect completion of a recognized engineering apprenticeship, diploma, or degree. As with most occupations, more middle and senior positions require experience.
Knowledge and Skills
An understanding of the oil & gas and power generation industries is important, as these are the industries where most of the machining opportunities are.
You should have strong technical knowledge and be able to interpret customer drawings and quickly grasp dimensions, tolerances, and customer requirements. Some basic analytical skills will be needed to deal with machining variances and problem-solving. The oil and gas and power generation industries are highly regulated so working to ASME standards is expected.