What is Stress-Free Temperature (SFT) in Rail Tracks and How is it Managed?
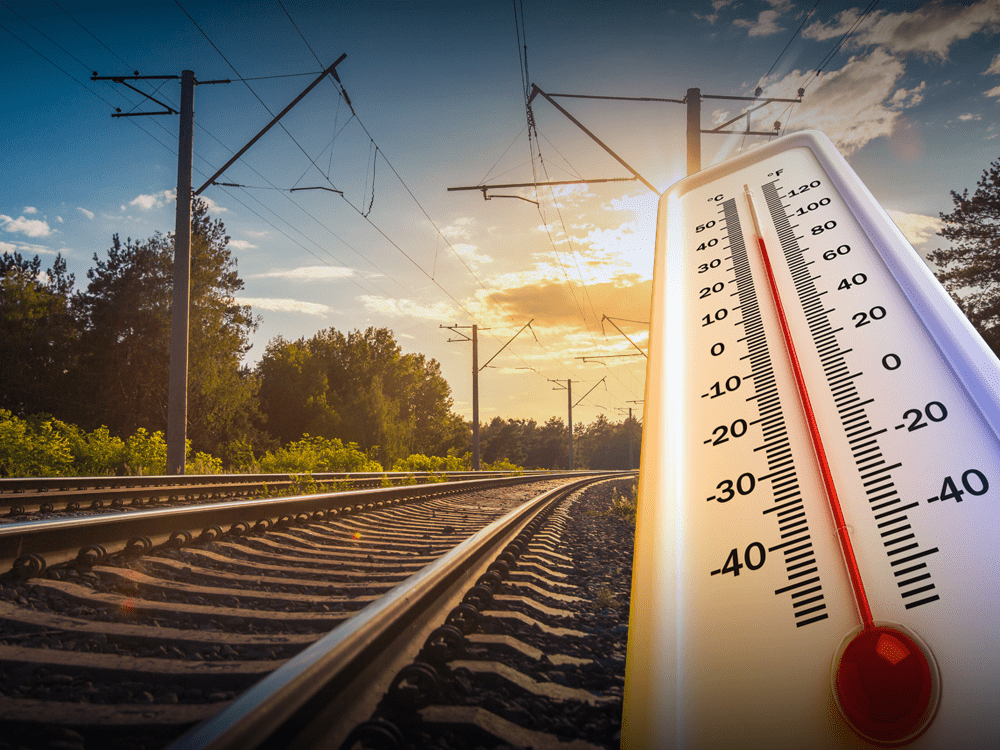
January 27, 2025
0
Stress-Free Temperature (SFT) is crucial in rail maintenance worldwide, especially where Continuously Welded Rails (CWR) are used. In some regions, this concept is known as Rail Neutral Temperature (RNT). So what exactly is SFT, why is it so important, and how is it managed?
Jump to section
- Evolution from Jointed Rail to Continuous Welded Rail
- How is SFT Set and Managed?
- Rail Stressing Process and Equipment Used
- RP70A Modular Rail Stressor
- The Future of SFT Management
In this article, we provide a simple overview of what SFT is, why it’s vital for rail stability, and how it’s managed. We’ll explore the factors that influence SFT, the technology used to measure and maintain it, and the challenges that come with using CWR systems. Finally, we’ll look at the latest innovations in rail maintenance, including non-destructive testing methods, rail-stressing equipment, and potential future advancements in the industry.
What is Stress-Free Temperature (SFT)?
SFT refers to the temperature at which the rail experiences no internal stress – neither tension nor compression. Excessive compression leads to track buckling (sun kinks), while too much tension can cause rail breaks. Both scenarios can have catastrophic consequences, making it essential to manage the rail near its SFT.
How SFT Varies Across the World
SFT values throughout the world are set based on local climate and operating conditions. For example, colder regions have lower SFT values, while hotter areas have higher ones. In the United Kingdom, the SFT is 27°C (80.6°F), whereas in parts of Australia and the United States, it can exceed 35°C, depending on the local climate. In countries with extreme seasonal temperature fluctuations, regular monitoring and maintenance are required to ensure rail stability.
The Evolution from Jointed Rail to Continuous Welded Rail (CWR)
Traditionally, rail sections were connected with bolts and fish plates to form jointed tracks. While functional, this system required constant maintenance due to the gaps between rail sections, which led to several issues:
- Increased dynamic impact on rail ends.
- Unwanted vibrations for passing trains.
- Increased stress on the ballast (the stones supporting the track) and the subgrade (the foundation beneath the tracks).
- Noise (that familiar “clickety-clack” sound).
All of these factors can accelerate wear, cause rail failures, damage sleepers (cross-ties), and lead to faster ballast degradation near the joints, resulting in the need for frequent maintenance and resulting in higher costs.
To solve these issues, engineers introduced CWR, where rails are welded together, eliminating most joints and their associated problems.
The Downside of CWR
Despite the many advantages of CWR, it introduces new challenges related to temperature-induced stress. As temperatures rise, welded rails may experience compressive stress, which can cause rail buckling if not properly managed. However, CWR remains the standard in modern rail networks due to its significant advantages over jointed rails.
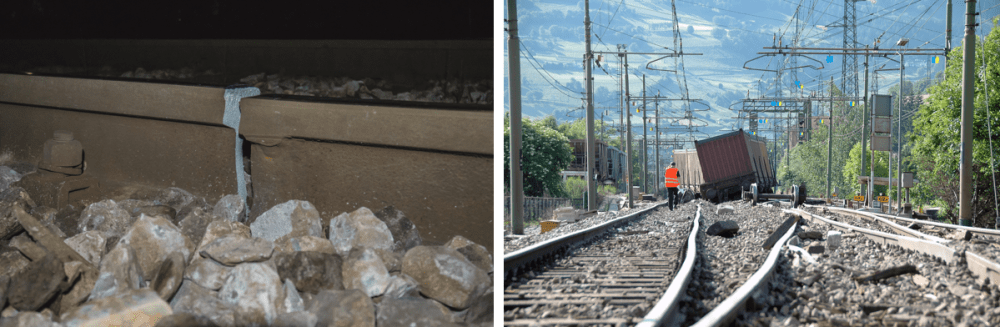
How is SFT Set and Managed?
Destructive Testing
Traditionally, stress-free temperature is measured by cutting the rail and assessing the movement and stress changes. Doing this accurately requires specialist technicians, equipment such as strain gauges, and thorough preparation.
Non-Destructive Testing
The more recent VERSE system eliminates the need to cut the rail, significantly reducing the time and cost of assessing track SFT. This system measures SFT directly from the installed rail without needing to know the residual stress at the time of manufacture. By using non-destructive testing, rail operators can survey tracks much faster than with traditional methods.
How it Works
To use this system, the rail temperature must be lower than its SFT so the rail is in tension. Taking a measurement requires around 30 metres of track to be unclipped. The VERSE frame sits on the sleeper (tie) and straddles the rail. The unit is clamped around the top of the rail and the rail is lifted using the built-in hydraulic jack. The rail is lifted to 10kN. The load and displacement outputs are transmitted to a hand-held computer, along with details of the rail temperature, rail profile, and its height. The software in the hand-held unit produces the SFT result.
How SFT Changes Over Time
Even when correctly set, various factors can alter the stress-free temperature of a rail:
- Frequent braking and accelerating of trains
- Track maintenance activities such as tamping
- Degradation of track fasteners and ballast
- Continuous temperature fluctuations
The Rail Stressing Process and Equipment Used
The stressing procedure typically includes cutting the rail, adjusting its length to match the target SFT, and welding the sections back together.
A rail stressor works by clamping around the rail track and using on-board hydraulic cylinders to pull sections closer together. These may be the pre-assembled type that uses PTO (power take of lines), lifted into position with a crane, or a modular design such as the Enerpac RP70A comprising of components that can be easily carried by the maintenance crew and quickly assembled on the track. This rail stressor requires a hydraulic power source such as the battery-powered ZC-Series. This pump offers a cleaner emissions-free solution than petrol-powered alternatives.
The interactive image below shows the key features of both types of rail stressor.
Benefits of the RP70A Modular Rail Stressor
- Lighter design for easier transport and deployment: Up to three times lighter than similar tools. Features high-strength steel and aluminum components, easy to carry by one or two persons
- Rapid and intuitive assembly: Equipped with automatic locking arms, clamps, and grippers for tool-free deployment in just a few minutes.
- Rail Industry Certified: Meets Network Rail’s rigorous standards, ensuring durability, reliability, and safety. Over 200 units are already in use.
- Sustainable clean energy solution: Compatible with the cordless Enerpac ZC-Series hydraulic pump, offering a zero-emissions solution ideal for tunnels and residential areas.
What Does the Future of SFT Management Hold?
The rail industry can learn from advancements in sectors like marine, aerospace, and the military. Technologies like track imaging, sensors, AI, and robotics have great potential to revolutionize maintenance practices.
Track Imaging and Sensors: Advanced camera and laser systems mounted on inspection vehicles and drones.
Artificial Intelligence: AI can analyze imagery, sensor data, and historical maintenance records to identify patterns, trends, and anomalies, helping detect potential defects before they worsen.
Innovations in Materials: The steel rails of today have evolved significantly from the first cast iron rails. Advanced alloys and refined steel compositions have improved rail performance, allowing them to withstand heavy loads and environmental stress better. Metallurgical advancements will likely continue, enabling rails to handle dynamic loading from passing trains without developing cracks.
Summary
Understanding and managing Stress-Free Temperature (SFT) is essential for ensuring the stability and safety of Continuously Welded Rail (CWR) systems. As rail networks continue to evolve, maintaining the correct SFT helps prevent issues like rail buckling or fractures caused by temperature fluctuations. Advances in technology, including non-destructive testing methods and innovative rail stressing equipment, are making SFT management more efficient and cost-effective. Additionally, future developments in materials, AI, and sensor technology will further enhance track maintenance, improve rail durability, and reduce the need for manual intervention. By adopting these innovations, the rail industry can continue to deliver safer, more reliable infrastructure for the future.
Learn More About Enerpac Track Maintenance Tools.
Resources
Science Direct YouTube LinkedIn