The Rail Stressor: Taking the Stress Out of Track Maintenance
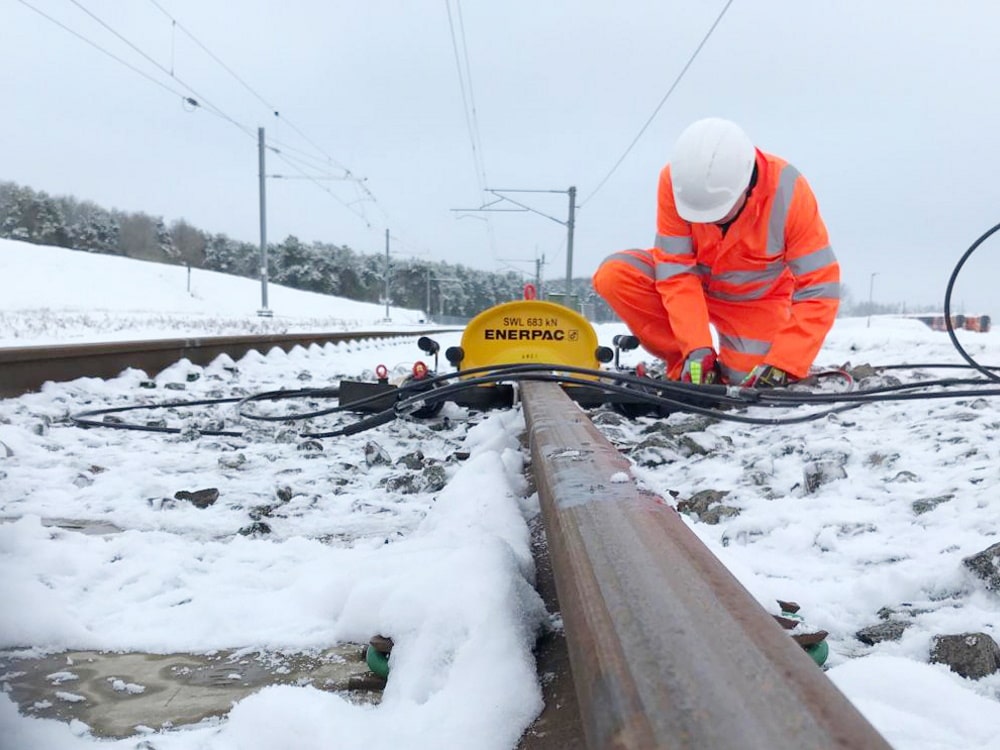
July 26, 2021
0
A rail stressor, also known as a rail puller, or a rail tensor, is a vital piece of equipment used by railway maintenance engineers for carrying out rail stressing, welding, failure repairs, and servicing.
They work by clamping around the rail track and use hydraulic cylinders to pull sections closer together. Although regarded as a specialized piece of equipment, there are different rail stressors available from several manufacturers throughout the world.
If you’re looking to buy a hydraulic rail stressor, what are the considerations? And what features should you look out for?
Let’s take a look at six key considerations.
Carrying the rail stressor to the trackside
In many instances, access can be a challenge. Even if a road runs alongside a track, the likelihood is you will not be able to get a truck-mounted crane exactly where you need it.
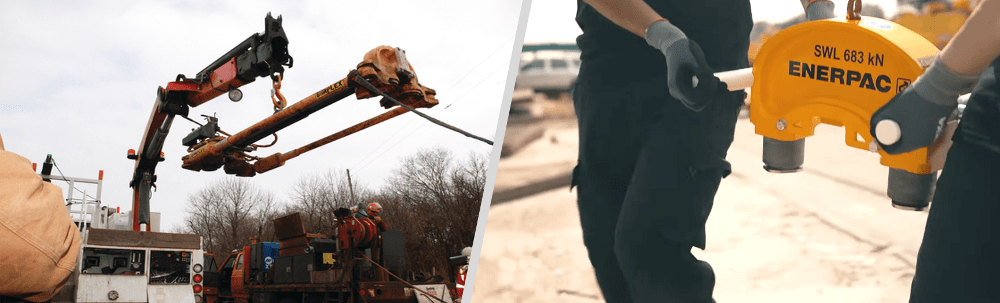
An assembled rail stressor can weigh well over 200kg (441lb). So, getting a fully or partially assembled unit to the track can be a struggle. This usually means a group of people will be needed to lift and assemble the unit with and several trips up or down the railway embankment. These all-in-one rail pullers remain popular in some countries such as the United States and work in a different way to the latest modular pullers. Instead of a hydraulic pump they link up to a PTO line (power take-off) which means they receive power from a motorized vehicle nearby. An example rail puller of this type is the RP120BP available from Enerpac.
In some regions throughout the world, manual handling guidelines specify that a person should not carry weights exceeding 25kg – (and that’s when holding the load close to the body at elbow height). Below or above the elbows or further away from the body, the recommended weight limit is less.
So before committing to buy a rail stressor, take a look at how it can be assembled and check the weights of each module. The weight should be clearly marked on each module and state whether a single or 2-person lift is needed. Lift Handles finished in a different color to the rest of the product are an added bonus.
Durability
The very nature of rail maintenance work means you’re most likely to be working outdoors. So, products will be put through their paces both when in use and during transportation. Welding splatter is inevitable, but damage to key components such as the hydraulic cylinders can be minimized by tough surface finishes and protective sleeves.
Rail Stressor Assembly
As already mentioned, one-piece rail stressors are too heavy to carry manually so very often, trackside assembly will be needed. Time is money, so consider a puller designed for easy and quick assembly. As an example, the Enerpac RP70A Rail Stressor can be assembled in as little as 2 minutes.
Powering the Rail Stressor
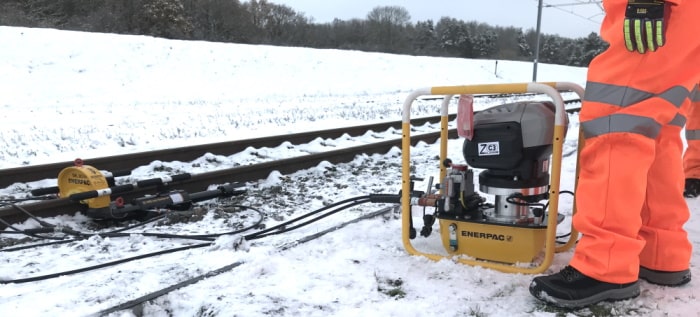
If you already own a hydraulic pump, is it compatible with the stressor and up to the job? When selecting the right pump, as well as output, consider weight, convenience, enclosed places such as tunnels and the environment. Low noise battery-powered pumps are available that operate below 80dBA max noise level with zero emissions.
Storage and Transportation
If you’re investing in a new rail stressor, you will want to protect your asset and keep all components together so nothing goes astray. A wooden crate is unlikely to stand the test of time, but a galvanized metal storage crate is ideal and will help extend its lifespan.
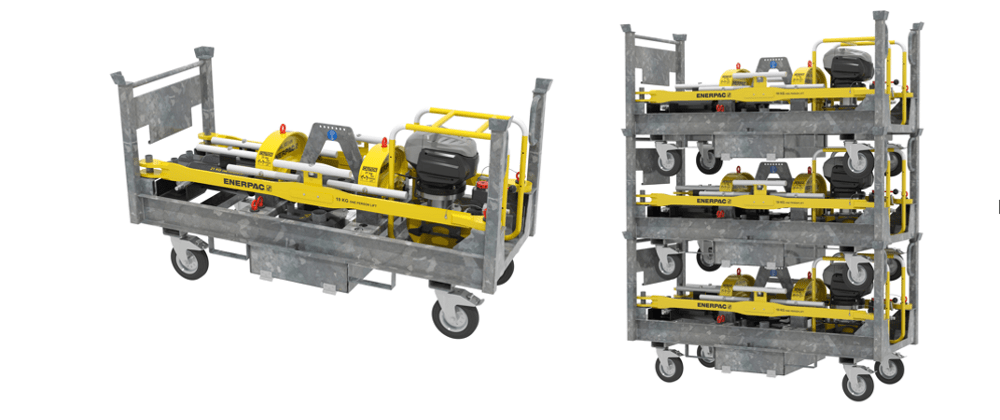
The example above shows a stackable transport frame with a box underneath to store hydraulic hoses. Wheels also help to move the equipment when a forklift is not available.