Predictive Maintenance: Definition and Benefits
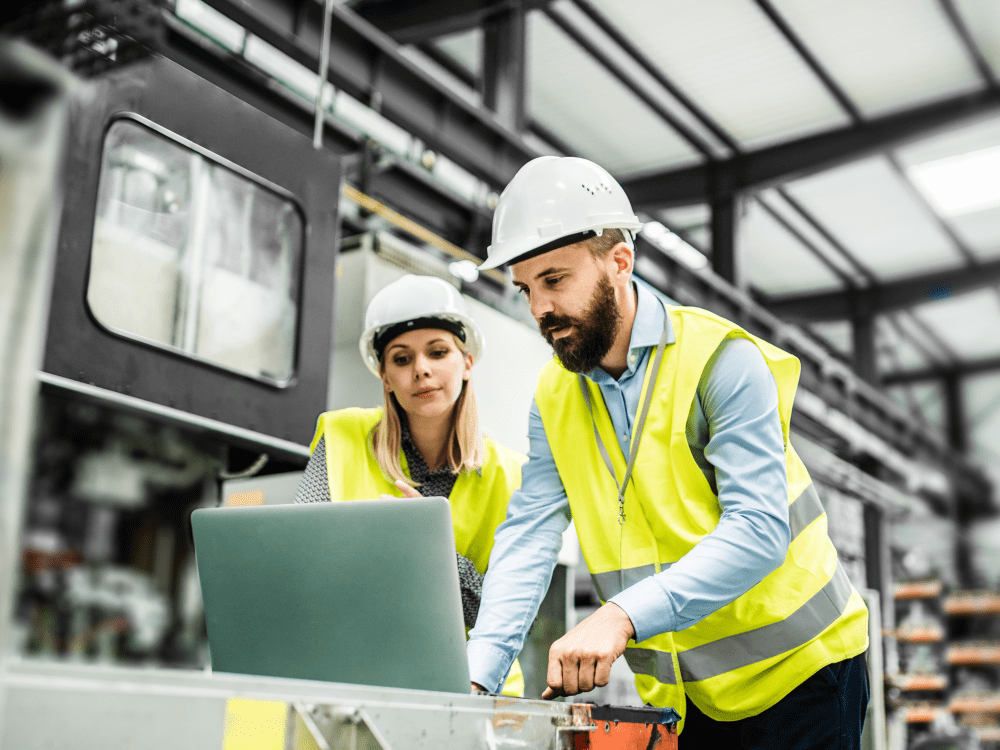
February 23, 2023
0
Predictive maintenance is a proactive approach that uses data and analytics to predict when equipment failures are likely to occur, allowing maintenance to be scheduled before a failure occurs. This strategy can help companies save money, reduce downtime, and increase equipment reliability.
In this blog post, we provide you with an overview of predictive maintenance, highlight some of the key benefits, share examples of predictive maintenance in practice, and introduce you to the Enerpac range of industrial tools that are suitable for maintaining and repairing your equipment.
What is Predictive Maintenance?
Predictive maintenance (PdM) is a maintenance strategy that uses data, machine learning, and analytics to predict when equipment is likely to fail, and schedule maintenance before a failure occurs. This approach is different from traditional maintenance strategies, such as preventive maintenance, which schedules maintenance based on time or usage, regardless of the condition of the equipment.
PdM uses various data sources to monitor the condition of equipment, including vibration, temperature, pressure, and other performance metrics. This data is then analyzed using machine learning algorithms to detect patterns and anomalies that could indicate an impending failure.
Benefits of Predictive Maintenance
PdM can provide several benefits to organizations, including:
- Reduced downtime: By identifying potential issues before they occur, organizations can reduce downtime and ensure that critical equipment is always available when needed.
- Lower maintenance costs: By performing maintenance when it is needed, rather than waiting for a failure to occur, organizations can reduce the costs associated with reactive maintenance.
- Increased equipment reliability: Predictive maintenance can help to improve equipment reliability by identifying potential issues and allowing maintenance teams to address them before they become major problems.
- Extended equipment life: By performing maintenance proactively, organizations can extend the useful life of equipment, reducing the need for costly replacements.
Is Predictive Maintenance Right for Your Business?
Predictive maintenance can deliver clear benefits but is not the optimum maintenance strategy for all companies. It requires investment in technology and manpower, so if your business doesn’t have expensive equipment or strict health and safety standards, a preventive (scheduled) maintenance program may be a better approach.
The following questions can help your decision:
- What is the approximate value of our equipment?
- What do your records show regarding equipment downtime, defects, losses, customer dissatisfaction, and safety threats?
- Is this approach really necessary for your organization’s type of machinery?
- What sort of predictive maintenance equipment would be best for our business’s needs? – ( e.g sensors for vibration, acoustic, infrared, motor circuit analysis, or oil analysis).
- Does my company have the financial resource to invest in predictive maintenance technologies and experts?
Examples of Predictive Maintenance
Predictive maintenance can be applied to different processes, regardless of the industry, the goal always stays the same. Types of analysis used in PdM include:
- Acoustic Monitoring: Much like an experienced maintenance engineer, AI is now capable of predicting machine issues problem by listening to its inner works. This method is not suitable in environments with lots of background noise.
- Vibration Analysis: A method that monitors changes in a machine’s vibrations. Normal vibration levels are determined, and managers are alerted only if a machine deviates from the regular levels.
- Infrared Technology: Checking the temperature of working machinery is another way to predict which machines are at risk of failure. This method can identify hot spots in mechanical and electronic equipment, and pinpoint which components and fuses, and electrical circuits are under stress.
- Motor Circuit Analysis: involves monitoring a motor’s stator and rotor to detect ground faults or contamination.
- Oil Analysis – Analysing machine oil and testing for wear particles, viscosity, and water, is common in the automation and transportation industry.
Example Applications of Predictive Maintenance
- Manufacturing: to avoid pushing machinery to the point of disruptive breakdowns
- Refrigeration sensors: used in the Food Industry
- Power generation: preventing power outages
- Utility suppliers: using huge amounts of data generated by smart meters to detect early traits of supply and demand issues
- Oil and Gas industry: to assess the condition and performance of valves, pumps, and pipelines
- Building management: for controlling humidity, ventilation, and temperature
- Aircraft maintenance: using sensors and flight data recorders to predict where irregularities may occur
Implementing Predictive Maintenance
Implementing a predictive maintenance program involves more than just adding sensors and then waiting for warning signs to show up. It requires a variety of steps, including data collection, data analysis, model development, and deployment.
Some key steps that organizations follow to implement a predictive maintenance program are:
- Identify the critical equipment that needs to be monitored and maintained.
- Install sensors or other monitoring devices to collect data on the performance of the equipment.
- Choose a predictive maintenance platform or software that can analyze the data and provide insights into potential equipment failures. A computerized maintenance management system (CMMS) is crucial for driving the maintenance aspect of predictive maintenance. It can create a work order for a technician to complete work whenever is appropriate.
- Train staff to interpret and act on the data and insights provided by the predictive maintenance software.
- Develop predictive models: Use the insights gained from data analysis to develop predictive models that can predict equipment failures.
- Deploy models: Once the predictive models have been developed, they need to be deployed in a production environment, where they can be used to monitor equipment and predict potential failures.
What tools are available to maintain and repair your equipment?
Aside from the tools and sensors used to monitor your machinery, your team will need high-quality industrial tools to complete maintenance tasks such as lifting, moving, dismantling, and reassembly. Hydraulic tools have the potential to significantly boost your productivity, thanks to their capacity to move heavier loads and exert greater force than mechanical, electrical, or pneumatic tools.
Tools for consideration include
- Hydraulic cylinder and pump sets
- Hydraulic torque wrenches
- Wheeled jacks
- Machine moving tools and equipment
- Lifting and spreading wedges
- Hydraulic pullers for removing shaft-mounted components
Conclusion
Predictive maintenance is a powerful tool for organizations looking to improve equipment reliability, reduce downtime, and lower maintenance costs. By collecting and analysing data, organizations can develop predictive models that can predict when equipment failures are likely to occur, allowing maintenance teams to perform maintenance proactively. While implementing a program can be challenging, the benefits it provides can make it well worth the effort.
If you’re investing in predictive maintenance systems, don’t overlook the possible need for the more productive tools that may be needed to carry out the actual maintenance work.