Cold Cutting Machines: Types and Applications
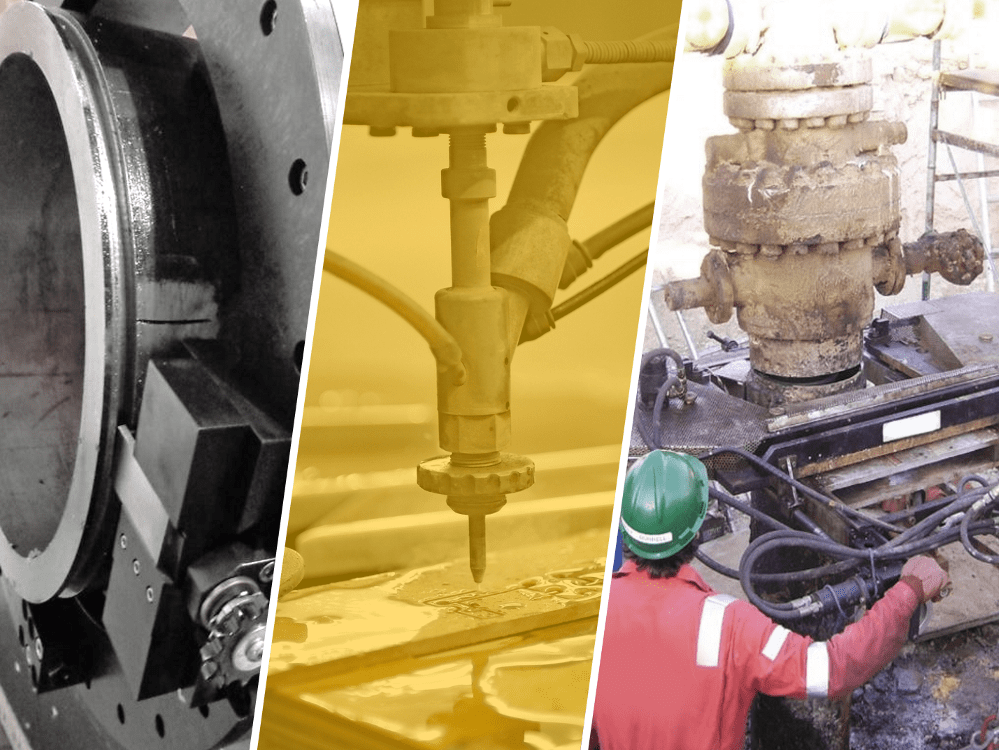
June 22, 2021
0
Cold Cutting Machines: Three Common Types
Three commonly used types of cold-cutting machines are pipe cold-cutting machines (aka clamshell cutters), cold-cutting saws, and abrasive water jet machines. But before we examine each of these, let’s clear up what cold cutting actually means.
What is Cold Cutting?
Cold cutting is a procedure used to cut through a material without using heat or a flame, and without producing sparks. This makes the process the safest method for cutting structures in hazardous environments. Typical industries where cold cutting is specified include oil & gas, materials processing, and petrochemicals.
Pipe Cold Cutting Machines
Pipe Cold Cutting Machines are also known by several other names. Most commonly clamshell cutters, split frame cutters, clamshell lathe, and other combinations of these words.
Pipe Cold Cutting Machines are circular in construction and wrap around the pipe in two halves attached together by a hinge.
When fully assembled, the machines work by rotating a cutting tool around the circumference of the pipe. The main purposes of the machines are to make either a straight or beveled cut in preparation for welding.
Different types include low profile, mid-size, and heavy-duty. They are available in sizes to suit all standard pipe diameters – even as large as 177” diameter. The machines are usually powered either from a pneumatic source or a hydraulic pump.
Benefits of Pipe Cold Cutting Machines
The two main benefits of a pipe cold cutting machine (clamshell cutter) are convenience and safety. There is no production of sparks, flames, or any airborne contamination. Additionally, there is no resulting HAZ (heat-affected zone), which can change the properties of the material.
Diamond Wire Saws
Diamond Wire Saws are used subsea for cutting through pipelines, piles, and caissons. Instead of a blade, a diamond wire saw uses a beaded rope encrusted with small diamonds on the outside surface. The circular cross-section of the ropes makes them less prone to the problems of compression and jamming sometimes encountered with metal blades. As with the band saw, when used topside (above the water’s surface), it is not a true cold-cutting procedure and coolant is required.
Decommissioning Saws are powered by hydraulics, therefore as suitable hydraulic power pack and hoses are also needed. The diamond wire saws can be attached to a subsea ROV (remotely operated vehicle) to maneuver into position.
Abrasive Water Jet Cutting
Abrasive Water Jet Cold Cutting is another method of cutting on-site structures without using a flame or heat. This makes the process well-suited to environments where there is a risk of fire or explosion.
This method uses an incredibly high-water pressure delivered through a small orifice at around 60,000 PSI (4137 bar). Within the water is a hard abrasive material, such as garnet, which is crushed so small that it passes through the nozzle of the water jet. Abrasive water jet cutting is not done using a hand-held device. Instead, the nozzle is mounted onto a carriage that moves across the surface to be cut.
The procedure will cut through any metal, concrete, or composite material. Example on-site applications include cutting apertures into vessels, storage tanks, or cutting large diameter pipework.
For cutting pipework, abrasive water jet cutting is less convenient than using a clamshell cutter, as the wastewater product needs to be dealt with. There is also the risk of causing damage to surrounding materials and coatings. However, this can be minimized by attaching a sacrificial plate to deflect any unwanted spray of the abrasive fluid.
Abrasive water jet cutting can cut very thick materials such as 6” (150mm) concrete slab and 4” (100mm) thick iron plate. The downside is that with greater thickness comes less accuracy. The further the nozzle is away from the point of contact the more likely the jet will cut diagonally and inconsistently.
Summary
So, which is the best cold-cutting method? It depends on what you are cutting, the location, and the accuracy needed.
For cutting and beveling piping the clamshell cutter is the clear winner. They’re easy to set up and there’s no risk of sparks being created.
For the purposes of decommissioning, a diamond wire saw is a good choice for cylindrical shapes – however, there is the risk of sparks being created if a suitable coolant isn’t used.
Abrasive water jet cutters are used widely during the manufacture of parts. However, they too have applications for decommissioning and onsite maintenance. With the right supporting structure built around the application, they can be used for cutting shapes into vessels or for severing iron girders and concrete structures.
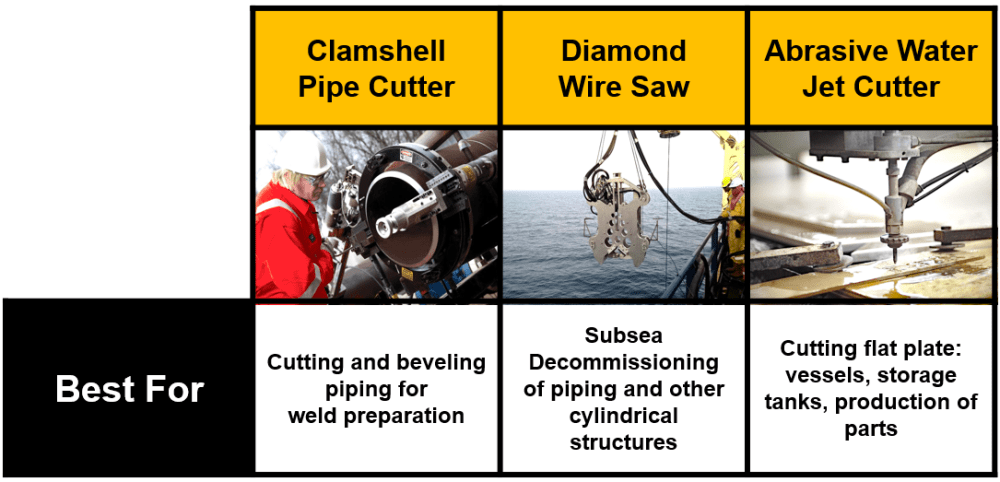