Offshore Wind Turbine Foundations: Leveling and Fixation with Hydraulic Cylinders
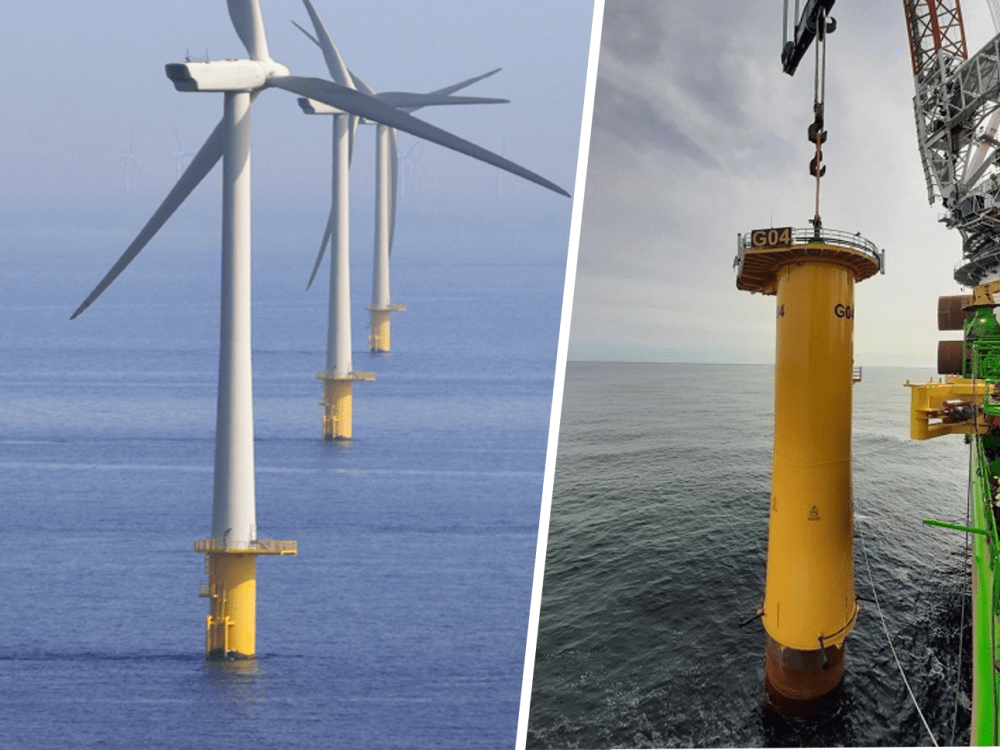
February 7, 2022
0
Offshore wind turbine foundations are built in various configurations, with one of the commonest being the monopile-transition piece foundation, (MP/TP).
MP/ TP Offshore Wind Turbine Foundations
These steel foundations are used in relatively shallow water (for depths up to 40m). They are one of the simplest types of foundation and round section steel piles, with a diameter of between 3.5 and 4.5 meters.
Depending upon the type of ground, the monopile is driven some 10 to 20 meters into the seabed – which provides a secure base for mounting the transition piece and the tower sections.
An important advantage of this type of foundation is that extensive preparation of the seabed is not necessary. Heavy-duty piling equipment is needed, and this foundation type is not ideal in locations with many large boulders in the seabed.
Leveling the Transition Piece
When you consider the height of these wind turbines and the forces they need to withstand, you can appreciate how important it is to make sure the transition piece is perfectly level. As well as providing stability and structural integrity, this will ensure the turbine generates maximum yield. The transition piece is fitted over the top of the monopile as shown in fig 1 below.
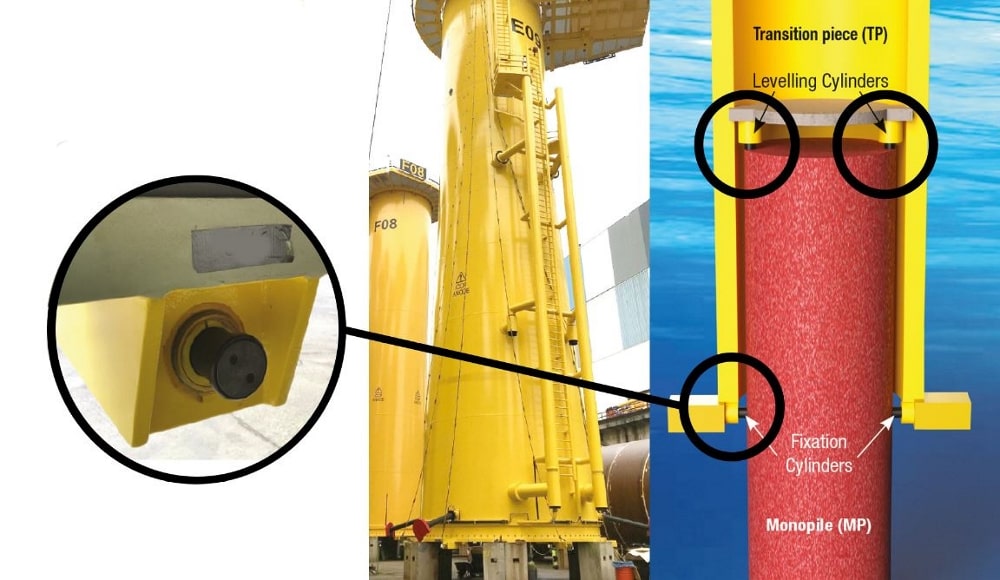
The leveling process is done using six to twelve pre-installed hydraulic cylinders attached inside the transition piece. Using hydraulic cylinders makes it possible to position the transition piece to a precise position – even if the monopile is not completely level.
The Enerpac hydraulic leveling system makes use of aluminum spring return cylinders. There are many variants available, and these can be provided with the required capacity and stroke to comply with the design of the application. The system will be supplied complete with fully compatible Enerpac hoses and HPU’s.
Fixation of The Transition Piece
Before the TP’s leave the manufacturing yard, six pre-installed horizontal positioned
hydraulic cylinders are mounted at the lower part of the TP for fixation during
installation and grouting.
The equipment connected to each cylinder usually contains
six twin hose-sets, including a hose cutter for each cylinder The fixation cylinders are
required to remain pressurized during the grouting process by a manifold.
These cylinders are operated subsea and plungers need to be retracted after
the hydraulic system is depressurized. Retracting the plunger is ensured by
activating the hose cutter and a reinforced return spring – eliminating the risk of point
load and contact corrosion with the MP.
Enerpac can provide a hydraulic fixation system, containing steel spring return cylinders
for subsea use, each with a capacity and stroke that complies with your design of the
application. The system can be supplied complete with Enerpac hoses and HPU’s.
Offshore Wind Turbine Foundation: Summary of the Leveling Process
- Before the transition pieces leave the manufacturing yard, the hydraulic cylinders are set up within the transition piece.
- The equipment connected to each of the cylinders is predefined between the design engineers of the T&I Contractor in cooperation with the TP Manufacturer and the Wind Support Team of Enerpac.
- Leveling takes place by activating the cylinders. All cylinders are required to remain pressurized during the grouting process by using a ball valve and holding the pressure.
- Once the transition piece is confirmed a level it is permanently fixed to the monopile by filling the annulus between the monopile and transition piece with high strength grout.
- The fixation cylinders are operated subsea, and the plunger on each needs to be retracted after the hydraulic system is depressurized to avoid steel to steel contact
- Retracting the plunger is ensured by activating the hose cutter and a reinforced return spring. This eliminates the risk of point load and contact corrosion with the monopile.
- Environmental considerations that are considered include the type of oil – for example, some specific project requirements may state the equipment is pre-filled the with water glycol or bio-degradable oil.
Preventing Subsea Oil Spills
The quantity of oil used in a small number of hydraulic cylinders may seem small when compared to oil spills from offshore oil and gas operations. But even a small amount can cause harm to wildlife and marine ecosystems.
An alternative system besides cutting the hoses subsea and to avoid any leakage from transition piece fixation can be achieved using a Remote Hose Disconnector®
The Enerpac Remote Hose Disconnector® RHDC is tested, witnessed, and certified by Lloyds till 100 meters subsea and can be reused.
The advantages of this system are:
- No oil spill in the sea during disconnection
- No need to use a hose cutting tool
- No waste of materials
- Repeatable use
Please contact Enerpac to discuss this system and for other equipment for wind turbines.
Related Case Studies:
Installing Offshore Wind Turbine Base Foundations with a SyncHoist System
Trolley System Speeds Up Offshore Wind Transition Piece Load Out
Foundation Created for Offshore Wind Turbines