Wind Turbine Blade Manufacture: How Orbital Milling Machines Can Help
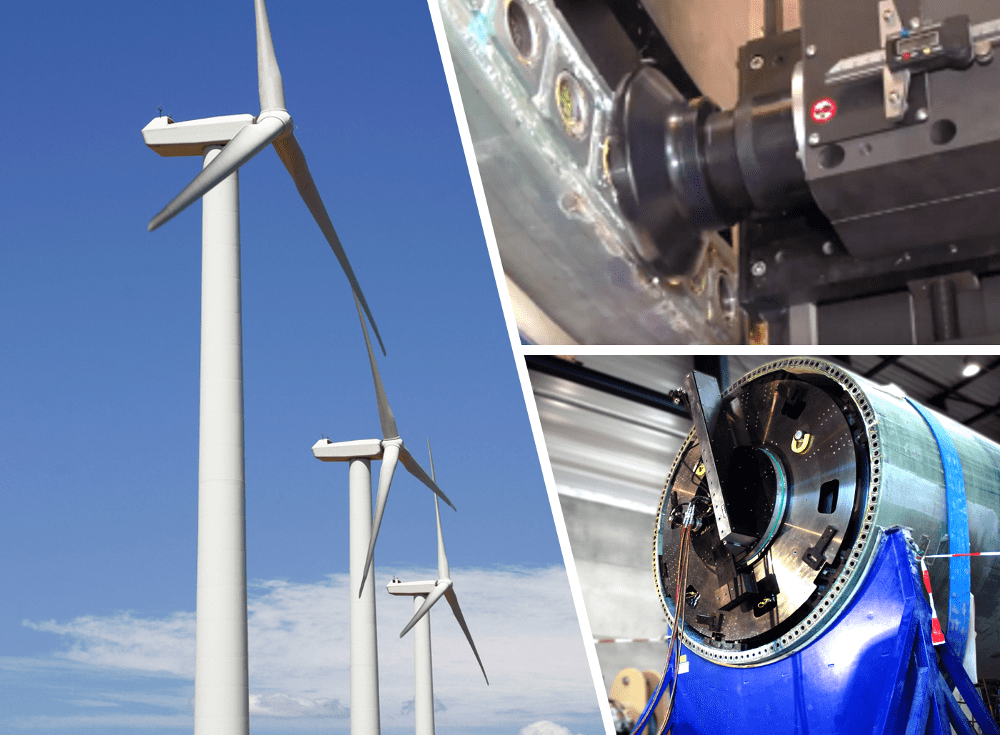
August 9, 2021
0
It will come as no surprise that the growing focus on environmental sustainability is driving increasing demand for wind turbines. Those involved in wind turbine blade manufacture can expect this trend to continue.
One forecast by Research and Markets, published in 2020 predicts that the global value of the market will reach more than US $123 billion by 2025. That’s an increase of more than $33 billion as compared with 2019.
This is good news for those in the business of wind turbine blade manufacture, who will look to increase efficiencies and the quality of the components they make. One machine playing a key part in these improvements is the orbital milling machine.
Let’s look at why they’re needed and how they work.
Orbital Milling Machines for Wind Turbine Blade Manufacture
Wind turbine blades are typically made from composite materials, which can result in an uneven surface at the root end of the blade. With this section of the blade connecting to the hub – accuracy is critical. A connecting surface that isn’t completely flat and smooth can seriously affect performance. In a worst-case scenario, the blade’s construction integrity could be impaired. An orbital milling machine can remove unwanted material from the blade root end to improve flatness and enable a secure connection.
How Orbital Milling Machines Work
First, the orbital milling machine clamps within the end of the turbine blade. A hydraulic system is then used to rotate the cutting arm, which travels around the full diameter of the turbine blade.
Power is provided from a hydraulic power pack via hoses connected to a central distribution hub. Mounted onto the end of the arm is a rotating milling head. This is the module that removes any unwanted material, leaving a flat and smooth surface. The machine is controlled at a safe distance using a pendant.
Orbital milling machines are large – with many being more than 3 meters in diameter. Although designed specifically for the wind power industry, they make use of standard components such as milling heads which can be easily replaced. Optional accessories include an industrial vacuum for the removal of dust and swarf.
Machining an average-sized blade takes around 30 minutes.
How Accurate Are The Results?
Often the engineering team behind the rotor blade will set the flatness tolerance in conjunction with the general manufacturer. Commonly accepted tolerances in the industry are global flatness of 0.33 mm around the diameter and local flatness of 0.05 mm within 12-15” of the radial.
How Do Orbital Milling Machines Attach to the Wind Turbine Blade?
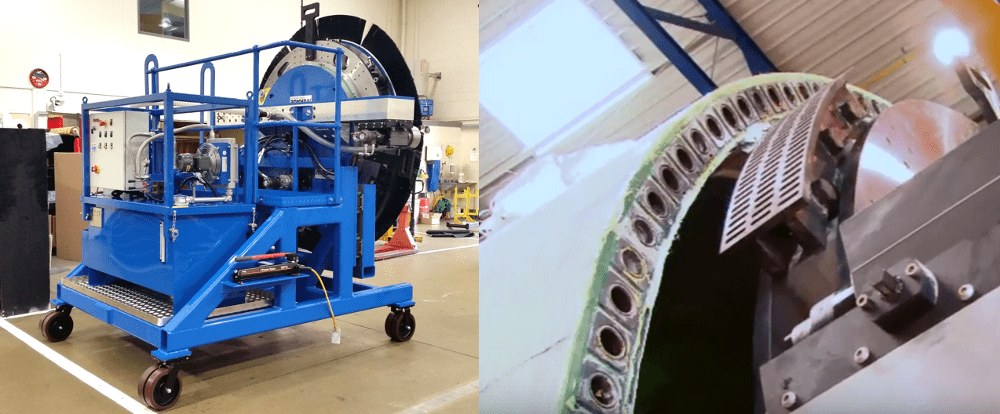
As with any manufacturing process, efficiency is key. The large size of turbine blades makes them hard to move around a factory. Depending on a crane to bring the rotor blades to a machine to be worked on one by one is not an option. Instead, an orbital milling machine is moved around the factory to each rotor blade using a purpose-designed trolley.
When in situ, the base of the machine is secured within the inside diameter of the blade using a hydraulic clamping mechanism. When fixed securely to the turbine blade trolley is detached and wheeled away while the machining takes place.
Looking to the Future
The amount of energy a turbine can generate depends not only on wind speed but also on the size of the wind turbine and the length of its blades. As the wind sector matures and the expertise of manufacturers increases, turbine blades are now being manufactured in much bigger sizes – some as long as 120 meters in length!
Larger orbital milling machines are now being developed to meet these needs. Some with more sophisticated controls to provide early warnings, such as notifying the operator when the cutters run out or alerting if there is any unacceptable movement.