Flange Face Corrosion: Identification and Repair
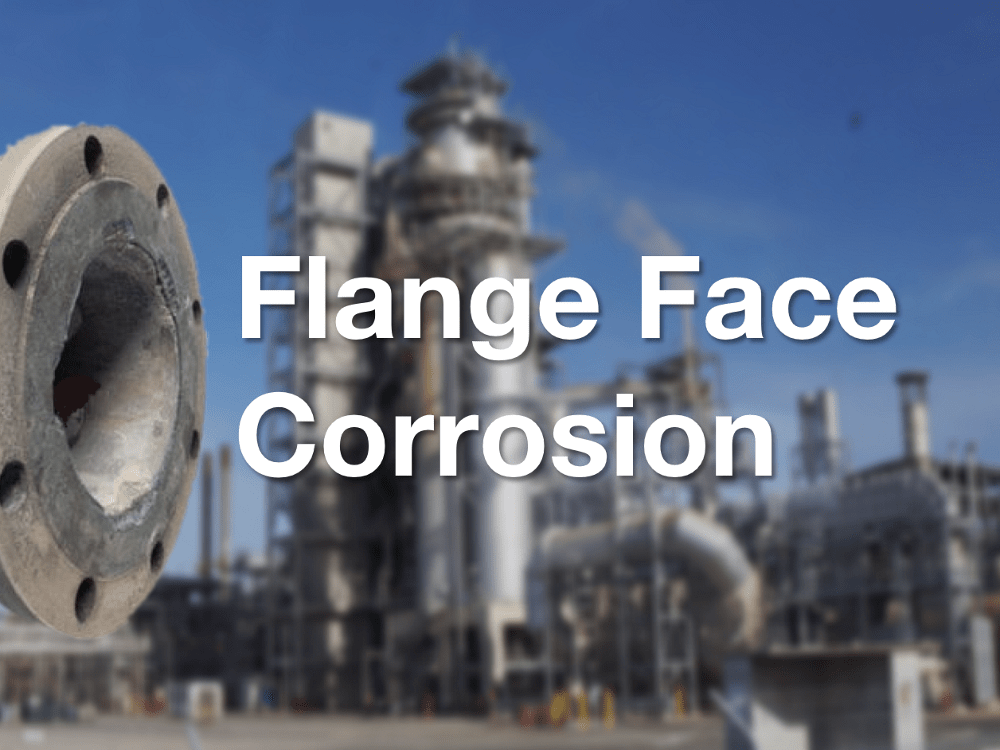
August 25, 2016
0
The Problem of Flange Face Corrosion
Piping systems in petrochemical refineries and oil & gas installations rely on hundreds of bolted joints which are exposed to corrosive conditions.
To ensure safe operation at these plants it is vital to carry out a regular inspection to assure joint integrity is maintained. Until recently, the normal procedure to do this was to physically disassemble each flange joint to check on its condition. Using this method was costly as it required shutdown and in many cases is entirely unnecessary.
Crevice and Flange Face Corrosion
Crevice corrosion is the bugbear of the oil and gas industry and is caused by a build-up of concentrated corrosive substances in the small confined area between two adjoining flanges. Because of this concentration, the rate of corrosion is much faster than elsewhere.
Environments containing seawater, acid, or H2S are especially problematic, putting the flange face and the joint’s integrity at risk with potentially serious consequences.
In addition to crevice corrosion, flange face corrosion is also widely recognized as an integrity issue, due to the potential leak path created by the break-in line. This can be in the form of small pits, often appearing in clusters on the flange’s sealing face.
Flange Face Inspection
As mentioned above, to disassemble a flange joint requires considerable cost in terms of both man-hours and shutdown time, but technology now exists to enable non-invasive checks to be carried out while the pipe joint is still in service.
Phased Array technology is now used by specialist inspection companies to identify the condition of the flange face gasket seating surface condition.
This uses ultrasound technology, but with multi-element probes to modify beam properties such as angle, standoff distance, and focal properties. Phased array inspection is now growing in popularity thanks to its flexibility and the compact size of the units now commercially available.
When inspecting the raised flange face area, encoded magnetic scanners direct sound from the OD of the flange between the bolt holes. The ultrasound angles can be adjusted to fit the specific flange geometry and the multiple ultrasound angles are used to optimize data displays of corrosion and/or erosion. The image above left shows a flange in good condition with a normal reflective corner pattern. On the right, the pattern is more haphazard and does not show a corner reflective pattern
How Corroded Flanges Are Repaired?
When a flange face is damaged it is no longer sealable by a gasket and should be either replaced or repaired.
In general, there are four basic types of repair to consider
- Removing the corroded flange and welding a new one
- On-site machining of the sealing face or ring groove within the flange tolerance
- Add material (Weld buttering runs) and site machining of the sealing face or ring groove
- Use of polymer composite repair materials to rebuild the flange face
What Portable On-site Machines Can Help?
Machines For Flange Face Repair
To machine the flange face sealing surface, a flange facing machine is the ideal product to get the job done quickly and accurately. Mirage Machines manufacture a wide range of machine options, including models that can be mounted internally or externally (and in some cases both). Smaller machines can be used for facing diameters as small as 2” with the largest being capable of facing up to 120” diameter.
In addition to machining a conventional flat sealing face, many machines can be used with various attachments or conversion kits for machining compact flange joints and RTJ grooves.
Machines For Flange Removal
When repair of the flange is not possible, the remaining option is to remove the flange entirely. This can be carried out using a split frame/clamshell pipe cutter. As the name suggests, the machine comprises of two sections that are fixed together and clamped around the pipe diameter.
To discuss your next project get in touch with a technical contact for your region here
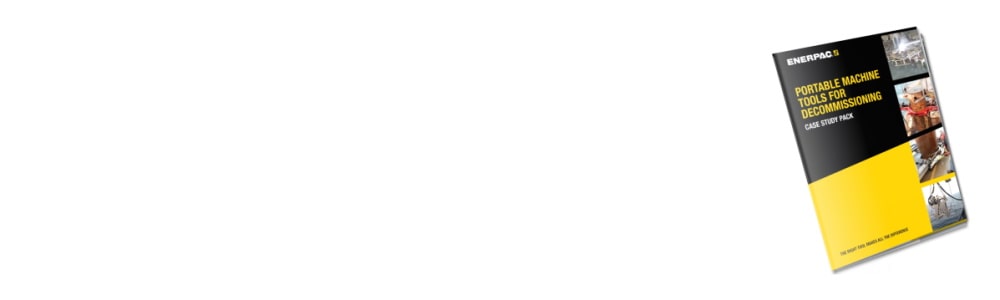
Decommissioning Case Study Pack
Learn how portable machine tools solved four tough decommissioning challenges