Guide to Flange Face Finish Types
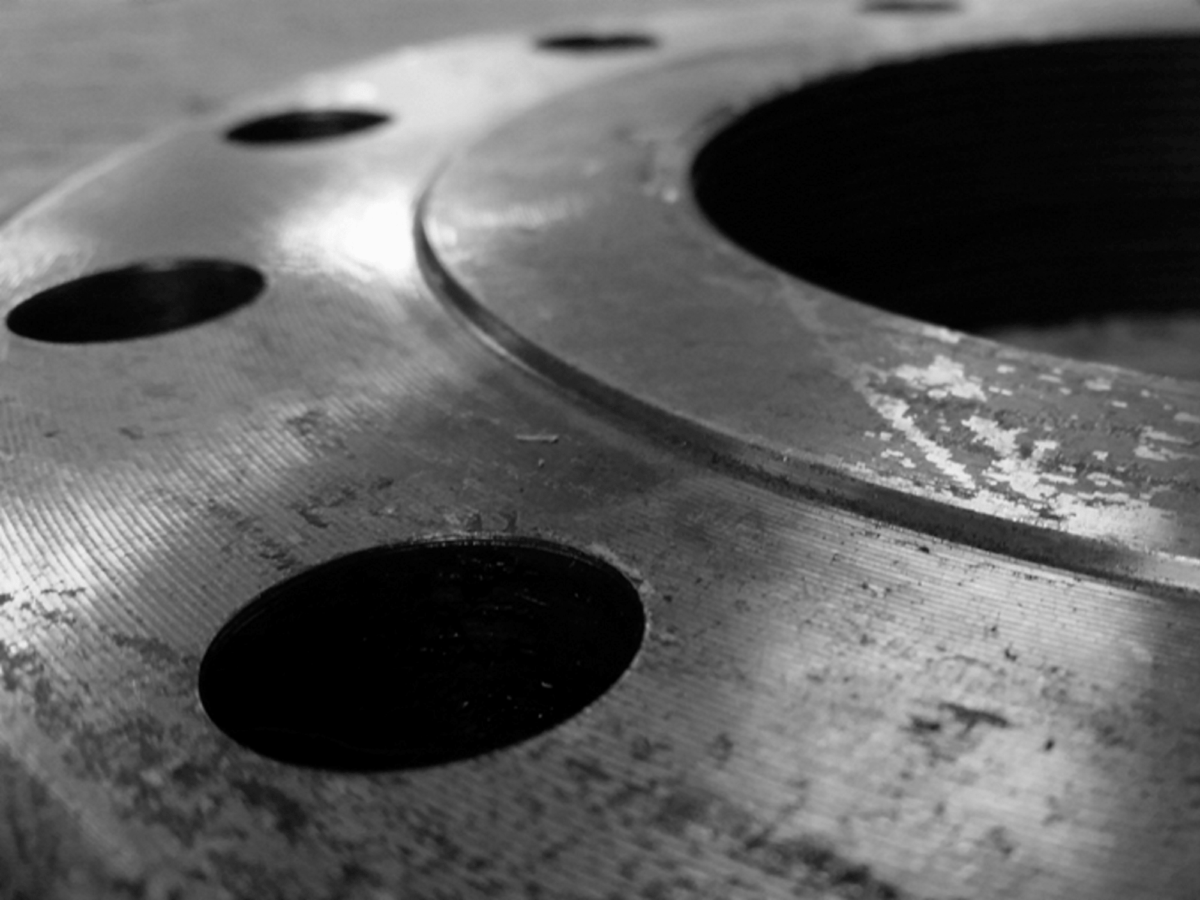
February 12, 2013
0
The American Society of Mechanical Engineers (ASME) has been around for over 130 years and is the standard-setter for mechanical engineers in over 100 countries around the world. ASME set the standards for flange face finish types through the ANSI accredited ASME Standard B 16.5 ensuring all gasket and flange fittings are consistent and fit for purpose allowing a high-quality seal.
Below are the standard surface finish types as determined by ASME.
Before you read on you may wish to subscribe to receive alerts when we post similar information. Simply subscribe using the button below.
Stock Finish
The stock finish is typically required for flange facings that will be in direct content with a gasket. The gasket contact surface is crafted using a continuous spiral groove (often referred to as phonographic) using a 1.6mm radius round-nose tool with a feed rate of 0.8mm per revolution and a depth of 0.15mm. This will result in a finish with a roughness between Ra 3.2 and 12.5 micrometers (125 – 500 microinch). The stock finish is suitable for most general surface conditions.
Smooth Finish
Flange faces with a smooth finish should show no apparent sign of tool markings when viewed with the naked eye. These finishes are often used for gaskets with metal facings such as double jacketed, flat steel and corrugated metal. As with the stock finish, this is achieved by having the contact surface machined with a continuous spiral groove generated by a 0.8mm radius round-nosed tool at a feed rate of 0.3mm per revolution with a depth of 0.05mm. This will result in a roughness between Ra 3.2 and 6.3 micrometers (125 – 250 microinch).
Cold Water Finish
Surfaces using a cold water finish are not usually intended to be used with a gasket, meaning the flange faces will be in direct contact. This finish is equivalent to a ground surface as it uses high-speed machining with a wide tool. The end result is a finish that is exceptionally smooth and mirror-like in its appearance.
Spiral Serrated Flange Face Finish
As with the stock finish, the spiral serrated finish uses a continuous spiral groove around the face. However, unlike the round-nosed tool used in the stock finish, spiral serrated finishes have a groove that is typically generated using a 90-deg tool. This creates a more prominent “V” geometry with 45° angled serration. Finishes of this type are created using a flange facing machine.
Concentric Serrated Flange Face Finish
Concentric serrated finishes use the same tooling at the spiral serrated finish although the grooves produced will be concentric grooves that are an equal distance apart rather than a continuous spiral groove. To achieve this a feed rate of 0.039mm per revolution with a depth of 0.079mm is most commonly used.